Micro Molding & Microfluidics - Overcoming Complexity Issues
HOW COMPOSITES BENEFIT THE TRANSPORTATION INDUSTRY
Trends for 3D Printing in Manufacturing
3D-Printed Concrete Could Drastically Change Construction Efficiency
LTG Lofts to go Makes 3D Printed Communities a Reality in Partnership with Black Buffalo 3D
Massachusetts Metalcaster Established Over a Century Ago Leaps Forward with 3D Mold Printing
Take Advantage of Current CNC Machining Trends
Tips to Save Money on Your Next CNC Milling Project
Calculating Injection Molded Plastic Part Shrinkage
The Potential of Polymer 3D Printing - Exploring Advanced Manufacturing Processes and Bearing Design
Metal Additive Manufacturing: The Cheaper the Better, asks IDTechEx
Successful use of Carbon-composite Windform® XT 2.0 and professional 3D printing in the construction of 1P PocketQubes flight-ready
When Should You Use 3D Printing for Production?
MICRO MOLDING FOR MICRO-ELECTRONICS
Smart Manufacturing Control
Records 181 to 195 of 779
First | Previous | Next | Last
Additive & 3D Printing - Featured Product
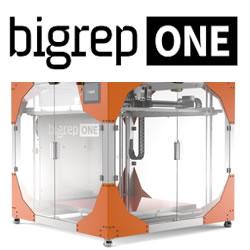