Navigating the future of metalworking in 2024 - Manufacturers turn to digitalised CNC machining and interconnected smart factories
Tezmaksan Robot Technologies looks at the key trends in manufacturing and explores why manufactures should embrace transformative technologies with user-friendly interface and adaptability to keep up with the evolving needs of the metalworking industry.
Metal Fabrication Shop Utilizes Efficient Production Method
When a client needs a prototype created quickly, longer-running fabrication jobs most likely will have to be be put on hold to make room for a rapid prototype manufacturing job.
Take Advantage of Current CNC Machining Trends
Understanding current trends in CNC machining is the first step to taking advantage of them. Here's what's changing and what it means for machine shops.
Axiomtek and FANUC America Case Study: Machining Simulator
The main purpose of the Machining Simulator is to promote learning about manufacturing in a classroom setting. Each simulator reacts exactly like a real machine and allows students to design, create CAD/CAM models and command the machine tool to produce simulated end product
The Rise of 5
Transitioning to 5-axis machining requires both a time and financial investment. But, like all investments, long-term it will pay off. The faster you begin to make the switch, the faster you will start to see the benefits.
Records 1 to 5 of 5
Featured Product
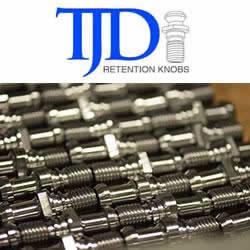
T.J. Davies' Retention Knobs
Our retention knobs are manufactured above international standards or to machine builder specifications. Retention knobs are manufactured utilizing AMS-6274/AISI-8620 alloy steel drawn in the United States. Threads are single-pointed on our lathes while manufacturing all other retention knob features to ensure high concentricity. Our process ensures that our threads are balanced (lead in/lead out at 180 degrees.) Each retention knob is carburized (hardened) to 58-62HRC, and case depth is .020-.030. Core hardness 40HRC. Each retention knob is coated utilizing a hot black oxide coating to military specifications. Our retention knobs are 100% covered in black oxide to prevent rust. All retention knob surfaces (not just mating surfaces) have a precision finish of 32 RMA micro or better: ISO grade 6N. Each retention knob is magnetic particle tested and tested at 2.5 times the pulling force of the drawbar. Certifications are maintained for each step in the manufacturing process for traceability.