Indian Aircraft Manufacturing Company Raphe mPhibr Revolutionizes Unmanned Aerial Vehicle Innovation with Dassault Systèmes' 3DEXPERIENCE Platform
Dassault Systèmes' 3DEXPERIENCE platform helped Raphe mPhibr reduce prototype development time from years to three months. The 3DEXPERIENCE platform integrates design, simulation and collaboration, supporting in-house design and manufacturing
Digital Twins in the Supply Chain: A Pathway to Predictive Logistics and Lean Operations
This article describes not only what a digital twin is but how it works as a predictive and resilient backbone for contemporary supply chains. From demand planning to warehouse automation, the revolution of the digital twin has already arrived.
Updates on Technology in Engineering: Digital Twins and AI Reshaping Product Development
Industry leaders like Dassault Systemes, Siemens, PTC, and Omnix International are pushing the boundaries of virtual twin experiences, AI-driven development, and immersive digital environments. Here is a look at some of the exciting updates in digital twins and engineering
These Innovations in Telecommunications Are Elevating Manufacturing in 2025
From 5G to edge computing, innovations are reshaping how factories operate and redefining smart manufacturing's potential.
Leveraging the Virtual Twin Experience for Decarbonization in the Metals Industry
In this article, Prashanth Mysore, Senior Director for Strategic Business Development at DELMIA, explores how Virtual Twin technology can transform your business operations, whilst also addressing decarbonization.
How XR is Accelerating Digital Twin Technology for Global Machine Hardware Manufacturers
Extended Reality or 'XR' is an umbrella term for Virtual Reality (VR) and Augmented Reality (AR). While digital twin technology has always helped to bridge the gap between virtual and physical realms, XR extends its capabilities several steps further.
ADLINK's AI Edge Server Successfully Deployed in Smart Manufacturing, Driving AI Innovation and Digital Transformation
Through real-time data analysis and intelligent decision-making, enterprises can simulate and predict production processes in a virtual environment, identify and solve potential problems in advance, and accelerate the pace of digital transformation.
The Future of Manufacturing: How Digital Twins, 3D AI, Robotics Automation, and Immersive Reality Tech Are Modernizing Industries
The manufacturing sector today is being driven by rapid advancements in sophisticated technology. Among the most significant contributors to this modernization are Digital Twins, 3D AI, robotics automation, and immersive reality technologies.
The Evolution of MQTT: Empowering Industrial Automation for 25 Years and Beyond
In manufacturing and industrial automation, the evolution of communication protocols has been pivotal in shaping operational efficiency, predictive maintenance, and overall innovation. Among these, MQTT stands as a beacon of connectivity
Using AI to Fill Blind Spots and Revolutionize Manufacturing Processes
One of the biggest pain points in the manufacturing industry is that most processes are not instrumented, resulting in upwards of 75% of digital blind spots. This lack of visibility on the shop floor leaves manufacturers without a complete data picture.
Navigating the future of metalworking in 2024 - Manufacturers turn to digitalised CNC machining and interconnected smart factories
Tezmaksan Robot Technologies looks at the key trends in manufacturing and explores why manufactures should embrace transformative technologies with user-friendly interface and adaptability to keep up with the evolving needs of the metalworking industry.
NVIDIA and Hexagon Deliver Suite of Solutions for Accelerating Industrial Digitalization
Sweden's Hexagon AB is connecting its reality capture and manufacturing platforms to NVIDIA Omniverse so enterprises can more easily develop and deploy digital twin applications.
What is Digital Twin technology and why is it important for manufacturers?
Whilst uptake in smaller manufacturing firms has been slower, those within the sector are slowly starting to see the value that digital twin technology can bring, no matter the size of the business.
Optimizing the Manufacturing Supply Chain With 7 Tech-Forward Solutions
Every manufacturing operation needs an efficient and resilient supply chain. Stock shortages, shipping delays and similar disruptions can prolong production, raise costs and impact customer satisfaction, so manufacturers must prevent them as much as possible.
How Simulation Can Secure Your Robotics Investment
Robotics simulation can be defined as a digital tool used to engineer robotics-based automated production systems. Essentially, robot simulation employs a digital representation to enable dynamic interaction with robot models and machines in a virtual environment.
Records 1 to 15 of 23
Featured Product
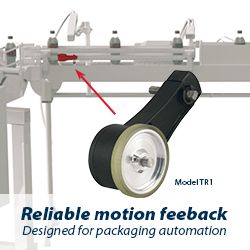
Model TR1 Tru-Trac
The Model TR1 Tru-Trac® linear measurement solution is a versatile option for tracking velocity, position, or distance over a wide variety of surfaces. An integrated encoder, measuring wheel, and spring-loaded torsion arm in one, compact unit, the Model TR1 is easy to install. The spring-loaded torsion arm offers adjustable torsion load, allowing the Model TR1 to be mounted in almost any orientation - even upside-down. The threaded shaft on the pivot axis is field reversible, providing mounting access from either side. With operating speeds up to 3000 feet per minute, a wide variety of configuration options - including multiple wheel material options - and a housing made from a durable, conductive composite material that minimizes static buildup, the Model TR1 Tru-Trac® is the ideal solution for countless applications.