Barriers to investing in CNC automation in 2025 - Transforming CNC automation obstacles into pathways for growth
Here Hakan Aydogdu, CEO at Tezmaksan Robot Technologies delves into these critical obstacles and reveals how innovative technologies and forward-thinking strategies are breaking down barriers, paving the way for a transformative shift in manufacturing.
Power Supply System Manufacturer Uses Tech to Revive Fabled Product Line
Entrepreneur Dan Klasel couldn't cope with the discontinuation of a line of mobile power supply systems, so he and his business partner bought it. Now, his team is modernizing its manufacturing through automation and manufacturing ERP software.
Metalworking Industry Sees Surge in Automation Adoption
While the basic steps in metalworking remain unchanged over the years, businesses increasingly rely on machines to complete them. While not unique to fabrication, this shift is seeing particular growth in the sector, so companies within the industry should pay attention.
Top Manufacturing Trends Looking Into 2025
The manufacturing industry thrives on competition. If you can keep up with the digital transformation, emerging technology, and workforce changes, you can leverage opportunities to boost operational efficiency and put competitors in your rearview mirror.
The importance of strong supply chains - Fast delivery drives efficiency in CNC manufacturing
One of the foremost ongoing obstacles is demand forecasting, where inaccuracies can lead to either stock shortages or excess inventory, both of which can have significant financial implications
Revolutionizing Machining Operations with Artificial Intelligence
The synergy between AI and CNC machining is set to reshape the future of manufacturing. Embracing these innovations will empower industries to achieve new levels of excellence, driving growth and success in an increasingly complex market.
The Manufacturing Talent Crunch and the CNC Machining Knowledge Capitalization
In this article, George Chen, DELMIA Senior Offer Marketing and Business Development Manager, takes a closer look at how advanced manufacturing could hold the key to addressing the skills gap in manufacturing.
The pool of operational excellence - CubeBOX Pallet Pool integrated with robust software maximises floor space
Limited floor space can hinder the implementation of new manufacturing technologies or the scaling up of production. Does this mean that manufacturers forced to operate within confined spaces should settle for suboptimal layouts
ZYCI: Manufacturing on a Mission
Supported by 15 Okuma machine tools (with more on the way), ZYCI has put Mitch Free exactly where he wants to be. He gets to work with the tangibles while creating noticeable, impactful changes within the manufacturing landscape.
Navigating the future of metalworking in 2024 - Manufacturers turn to digitalised CNC machining and interconnected smart factories
Tezmaksan Robot Technologies looks at the key trends in manufacturing and explores why manufactures should embrace transformative technologies with user-friendly interface and adaptability to keep up with the evolving needs of the metalworking industry.
The Future of Computer Aided Manufacturing & Fabrication
Playing a key role in ensuring that automation is incorporated into the fabrication process helps to keep things moving along as quickly and efficiently as possible for manufacturing businesses around the world.
Cyan Tec and FANUC bring MTC's vision of large-scale robotic laser cutting cell to life
A suite of automation solutions from FANUC has proved integral to the delivery of an industrial-scale laser cutting cell commissioned by the UK's Manufacturing Technology Centre (MTC). Constructed by system integrator
Choosing a Robotic Spindle for Deburring
The nature of the deburring task is highly repetitive, dirty, and carries a risk of injury. Retaining personnel for such a strenuous and messy job is challenging. Robotic deburring is an appealing option for these reasons, plus the results are more precise and repeatable.
Automated Support Removal & Finishing for Metal AM - Robots vs CNC
This article will address the transition to automated support removal (and finishing) solutions and consider the advantages and disadvantages of using CNC systems versus the versatility and reliability of robots.
What types of CNC machines will smart factories demand? Will software or hardware rule?
Different types of CNC machines will appear in smart factories. Here's what you need to know about
upgrading and updating your machines.
Records 1 to 15 of 61
Featured Product
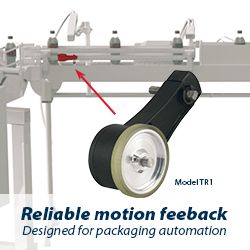
Model TR1 Tru-Trac
The Model TR1 Tru-Trac® linear measurement solution is a versatile option for tracking velocity, position, or distance over a wide variety of surfaces. An integrated encoder, measuring wheel, and spring-loaded torsion arm in one, compact unit, the Model TR1 is easy to install. The spring-loaded torsion arm offers adjustable torsion load, allowing the Model TR1 to be mounted in almost any orientation - even upside-down. The threaded shaft on the pivot axis is field reversible, providing mounting access from either side. With operating speeds up to 3000 feet per minute, a wide variety of configuration options - including multiple wheel material options - and a housing made from a durable, conductive composite material that minimizes static buildup, the Model TR1 Tru-Trac® is the ideal solution for countless applications.