Metalworking Industry Sees Surge in Automation Adoption
While the basic steps in metalworking remain unchanged over the years, businesses increasingly rely on machines to complete them. While not unique to fabrication, this shift is seeing particular growth in the sector, so companies within the industry should pay attention.
10 Areas Manufacturers Might See an Impact from AI
AI can be programmed to learn from the data ERP software gathers to make deeper and more accurate predictions regarding customers, buying habits, inventory levels, markets, material purchasing and more.
6 Reasons to Choose EDM Over Traditional Machining for Better Results
EDM - could be classified as one of the most useful in a modern shop. Also called a spark machining tool, the device uses sparks, or electricity, to cut through materials. It uses thermal energy to make the cuts by removing material.
Benchmarking Photo Chemical Etching for Precision Metal Applications
The unique characteristics of PCE overcome many of the issues associated with more traditional metal cutting technologies, and as such - in some instances - when looking for a cost-effective solution for the manufacture of precise metal parts, it is the only viable choice.
Records 1 to 4 of 4
Featured Product
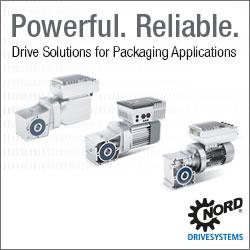
NORD Delivers Powerful, Reliable Drive Solutions for Demanding Packaging Applications
When you need quality, flexibility and high efficiency, NORD has you covered with complete drive solutions for primary and secondary packaging, end-of-line packaging, and higher-level applications. NORD supports you through the entire life cycle of your drive systems with pre-sales engineering support, online tools, and a global service network. Drive systems for both vertically and horizontally networked technology with all the options for sensor incorporation and integration into the higher-level control system.