Metalworking Industry Sees Surge in Automation Adoption
While the basic steps in metalworking remain unchanged over the years, businesses increasingly rely on machines to complete them. While not unique to fabrication, this shift is seeing particular growth in the sector, so companies within the industry should pay attention.
Waste not, want not - rapid identification of metals in scrap
Handheld devices, such as XRF analyzers, offer recyclers tools to rapidly and accurately determine the composition and grade of incoming scrap. This eliminates the need to depend on traditional verification methods such as spark or chemical tests.
THE RISE OF AUTOMATION IN METAL AM POST-PROCESSING - TRANSFORMING THE INDUSTRY WITH PRECISION AND EFFICIENCY
We delve into how automation in metal AM post processing is setting a new industry standard, and how companies like Rivelin Robotics are leading this change with their Netshape® Robots to unlock new productivity and efficiency gains.
Why 3D Metal Printing Is Key to the Future of Aerospace Engineering
The aerospace industry constantly pushes the boundaries of what's possible, and the demand for advanced manufacturing techniques has never been more critical. This pursuit of innovation has led to a significant shift toward 3D metal printing.
CLEANING UP AM'S DIRTY SECRET
The fact that post processing metal parts requires such intensive manual intervention throws up a series of follow-on problems. These include part-to-part quality inconsistencies, repetition fatigue, significant health & safety risks.
Metal Additive Manufacturing Launches Learning Experience on Rocket Turbopump Design
All eyes are on metal AM to reach the ideal of single-part rocket construction, where as many parts and sections as possible are combined for material integrity, maximum weight reduction, performance, and speed-of-manufacture.
Enhanced Quality Control and Post Processing for Metal 3D Printing
Metal 3D-printed parts can be produced at higher production rates with impeccable quality by implementing advanced quality control and post-processing techniques.
Metal Additive Manufactured Parts for Racing Car
In metal powder bed fusion process the quality and of the powder raw material are of paramount importance, as the process relies on thin layers of metal powder being deposited and melted to produce metallic parts.
Relativity Space Maps Path to Terran R Production at Scale With Unveil of Stargate 4th Generation Metal 3D Printers
Relativity Space's Stargate 4th Generation 3D metal printers, capable of horizontally printing objects up to 120ft long and 24ft wide at as much as 12x faster than its predecessor.
Metal 3D Printing Promotes Revolution in Valve Design and Manufacturing
The emergence and mature applications of metal 3D printing technology, as well as intelligent software such as CFD and CAE, are driving and leading new changes in valve design and manufacturing.
Metal 3D Printing Technology Landscape - IDTechEx Outline The Trends and the Whitespaces
Through an extensive benchmarking study, IDTechEx has asked the question: where are metal additive manufacturing technologies going, and where are the whitespaces for advancement in the metal AM landscape?
Benchmarking Photo Chemical Etching for Precision Metal Applications
The unique characteristics of PCE overcome many of the issues associated with more traditional metal cutting technologies, and as such - in some instances - when looking for a cost-effective solution for the manufacture of precise metal parts, it is the only viable choice.
How Will Labor Shortages Impact Metal Fabrication in 2022?
The American Welding Society estimates a 400,000-worker shortage by 2024. The urgent need for more welders and higher skill levels among welding personnel is widely known and accepted in the U.S. manufacturing industry.
Case Study: Keselowski Advanced Manufacturing (KAM)
Laser Powder Bed Fusion (L-PBF) is central to its production of metal additive manufacturing (AM) parts. In this process, lasers melt and weld layers of metallic powder resulting in parts that are durable and can be polished.
Improving the Performance of Supercritical CO2 in Next-generation Energy Applications with 3D Metal Printing
Mohawk Innovative Technology uses VELO3D's metal AM system to develop a high temperature heat transfer fluid circulator for the Department of Energy
Records 1 to 15 of 36
Featured Product
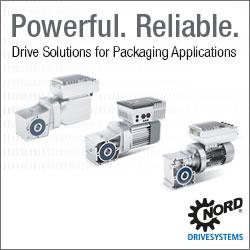
NORD Delivers Powerful, Reliable Drive Solutions for Demanding Packaging Applications
When you need quality, flexibility and high efficiency, NORD has you covered with complete drive solutions for primary and secondary packaging, end-of-line packaging, and higher-level applications. NORD supports you through the entire life cycle of your drive systems with pre-sales engineering support, online tools, and a global service network. Drive systems for both vertically and horizontally networked technology with all the options for sensor incorporation and integration into the higher-level control system.