Laser Powder Bed Fusion (L-PBF) is central to its production of metal additive manufacturing (AM) parts. In this process, lasers melt and weld layers of metallic powder resulting in parts that are durable and can be polished.
Case Study: Keselowski Advanced Manufacturing (KAM)
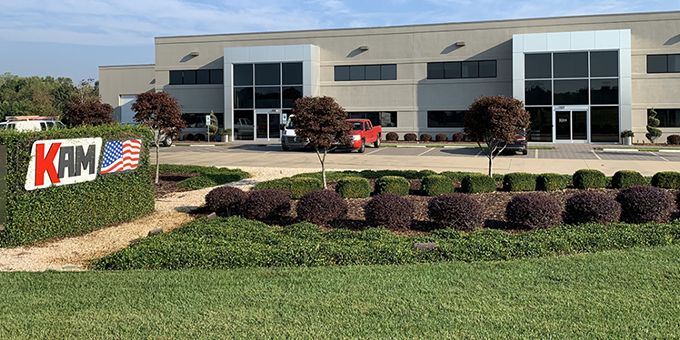
Case Study from | Essentium
SITUATION OVERVIEW
Headquartered in Statesville, North Carolina, Keselowski Advanced Manufacturing (KAM) is a pioneer in hybrid manufacturing. This new approach combines additive and subtractive technologies to solve traditional manufacturing problems and ultimately revolutionize the factory floor.
Among the array of state-of-the-art processes that KAM wields, Laser Powder Bed Fusion (L-PBF) is central to its production of metal additive manufacturing (AM) parts. In this process, lasers melt and weld layers of metallic powder resulting in parts that are durable and can be polished. After parts leave the L-PBF process, technicians machine features into the parts and send them through for inspection. During this refining stage, a Wire Electrical Discharge Machine (Wire EDM) removes any printed support material left on the part, and a Coordinate Measuring Machine (CMM) makes final inspections. As the parts go through these processes, fixtures hold them in the correct position f or speed and consistency. For machined parts with simple geometry, conventional fixturing methods suffice, but for highly detailed AM parts, fixturing can be more complicated.
THE CHALLENGE
In general, the more complex the surface of the part, the more detailed the fixture needs to be. In the past, skilled technicians at KAM used a clamping system to rig parts in place. This process was time-consuming and difficult to replicate for consistency.
The Wire EDM Challenge
During this step, technicians created precise manual rigs to ensure the Wire EDM made straight, repeatable cuts. Using this manual rigging method, technicians took an average of 25 minutes and 18 seconds to set up each part.
The CMM Challenge
Once the part was ready for inspection, it had to pass through the CMM. The average time it took technicians to rig parts for this step was eight minutes per part. Additionally, if the part had many features that needed to be probed by the CMM, it could require two runs, which doubled the set-up time. In a fast-paced facility like KAM, these limitations created huge bottlenecks for product orders.
THE SOLUTION
At KAM, employees are committed to continuous improvement for their customers and their internal processes. When the limitations of manual rigging became a problem, they knew that custom fixtures were the solution. After weighing the options, they found advanced support in Essentium’s High Speed Extrusion (HSE™) 3D Printing Platform.
The technicians at KAM quickly put their HSE 3D Printer to work and designed a fixture for the Wire EDM as well as the CMM. For these parts, they used Essentium HTN, a high temperature nylon, due to its printability, toughness, and wear resistance. The speed of the HSE 3D Printer allowed them to iterate through designs quickly to achieve the best features for the fixtures. Once the parts were designed and printed, KAM technicians used them on a product order of 25.
“Essentium HTN is our go-to material if we want to get a print right the first time. The printability of the material combined with the speed of the HSE 3D Printer allows us to quickly to iterate through designs, print them, and use them on the same day.” JOSHUA OSWALD, ENGINEER, KAM
Wire EDM Fixture
When using the Wire EDM fixture, the average set-up time for each part was two minutes and 34 seconds. Including design and preparation, the labor time came to a total of 2.4 hours for the product order, saving technicians 8.14 hours of labor.
CMM Fixture
The addition of the CMM fixture to the inspection process sped up the average set-up time for each part to zero minutes. After designing and preparing the part, the labor time came to a total of 2.25 hours for the product order, saving technicians 1.05 hours of labor. Additionally, all critical dimensions on the part were exposed, which ensured complete inspection on one pass.
BUSINESS OUTCOMES
In the end, the impact of swapping manual rigs for 3D printed fixtures was immense. For this product order, KAM’s use of 3D printed fixtures for the Wire EDM and CMM increased consistency and slashed labor time by 77% and 32%, respectively.
However, the positive outcomes didn’t end after the order was complete. In fact, KAM foresees that its custom fixtures can be used for future orders for the same part, saving even more time in the long run. Due to the speed of the HSE 3D Printer — which prints 5-15x faster than the competition — KAM will be able to quickly iterate through designs for future fixtures for complex product orders to come.
About Essentium, Inc.
Essentium, Inc. provides industrial 3D printing solutions that are disrupting traditional manufacturing processes by bringing product strength and production speed together, at scale, with an open ecosystem and material set. Essentium manufactures and delivers innovative industrial 3D printers and materials enabling the world’s top manufacturers to bridge the gap between 3D printing and machining and embrace the future of additive manufacturing
The content & opinions in this article are the author’s and do not necessarily represent the views of ManufacturingTomorrow
Comments (0)
This post does not have any comments. Be the first to leave a comment below.
Featured Product
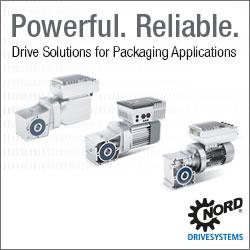