6 Reasons to Choose EDM Over Traditional Machining for Better Results
The average machine shop consists of dozens, if not hundreds, of various machines, some built for a specific purpose and others more versatile. During projects, operators generally swap between systems depending on what’s needed, like using a polisher to finish a piece or remove burrs, or a surface grinder to smooth the exterior.
One such tool – called an electrical discharge machining system, or EDM – could be classified as one of the most useful in a modern shop. Also called a spark machining tool, the device uses sparks, or electricity, to cut through materials. It uses thermal energy to make the cuts by removing material.
The reason it’s so special is that it introduces some relatively innovative manufacturing opportunities. It cuts through metal and hard materials with incredible precision and can produce complex shapes and contours. It’s not suitable for every job in the machine shop – but there are instances where it’s more beneficial to use EDM over traditional machining solutions.
Types of EDM Systems
As we see with most machines, there are varying types of EDM tools. Before looking at some of the tasks they can handle, it makes sense to explore the two types that currently exist:
Conventional EDM
A metal die is used as an electrode to produce a distinctive shape. That electrode is then impressed deep into the material that needs to be formed. This creates a negative impression of the unique shape and results in a mold. Conventional EDM machines also go by many other names, including sinker EDM, die sinking, cavity-type, volume, and ram EDM.
Wire EDM
A thin, heated wire is used as an electrode with hard diamond guides in place to hold the wire steady and stable. The taut wire is then used to cut through the material. While the wire doesn’t touch the surface of what it’s cutting – the electrical discharge does – the system still unspools new wire automatically to keep cuts smooth and seamless.
Both types of machines can be used to cut or shape incredibly tough materials such as tungsten, titanium, hardened steel, and other carbides. Traditional tools, especially blade-based, are woefully inefficient for cutting a lot of these materials.
So, when would electrical discharge machining be the better choice versus traditional machining techniques?
1. They’re Reliable and Efficient
Most machines, in general, are designed to be used in automated environments, at least for the bulk of their operation. However, that does not necessarily mean they are low-maintenance, or that they can be trusted to run indefinitely.
EDM machines, on the other hand, are less susceptible to errors or interruptions and can be left to run with minimal supervision, which makes them perfect for “lights out” manufacturing opportunities.
There are still some things to think about when automating on a continuous level – such as the replacement of electrodes – but it’s both possible and practical. Electrical discharge machining tools are reliable and efficient, which is great news for any manufacturer or machine shop administrator.
2. They’re Remarkably Precise
Even with some of the best precision in the industry, there are still machines that cannot be used in certain instances, like when creating sharp internal corners.
That is not true for EDM machines – especially the wire-based variants. When utilizing the appropriate type of wire, tension, and feeding, it’s possible to cut sharp and tight internal corners, and ultimately create shapes not possible with other methods. A sharp or square internal corner is difficult with traditional machines, for example, because cutting tools are generally round.
While a wire is technically round, the type of wire used in EDM machines is so small that it’s perfect for deep or sharp cuts, which is also beneficial when cutting internal corners or making incisions in existing pieces.
3. They Can Make Deep Cuts
The materials typically used in a machine shop are tough, strong, and incredibly challenging to work with. That means, with certain tools, the idea is to create designs that leverage shallow cuts and fine-tuned interactions – the goal is to minimize the work that needs to be done. EDM machines offer something completely different and they can make deep and large cuts in these pieces or materials.
What’s more, those cuts won’t result in noise, poor or inefficient seams, or troublesome divisions. In other words, the tool delivers a clean, reliable cut every time, regardless of how deep it needs to go. Not to mention, it doesn’t matter what material it is, whether that’s tungsten or a type of carbide.
4. They Make Strong Molds
Operators tend to prefer EDM machines over CNC machining when making molds because the technology can cut through incredibly strong materials, resulting in a tough mold with better longevity than something like plaster or plastic.
Sometimes, to create a mold, both machining techniques will be used, to first create the negative shape with a CNC mill, and then to craft more precise edges with a wire EDM.
It’s a fantastic way to develop an injection mold. And again, because the final mold materials are much stronger, it helps reduce costs – because they’re not replaced as often – but also allows for even more possibilities that aren’t possible with fragile or one-time-use molds.
When the EDM-created molds are combined with additive manufacturing processes, it’s possible to reimagine machining and production entirely.
5. They’re Ideal for Hard Materials
EDM machines can bore and cut through many materials, including some of the hardest in the industry. The toughness does not affect precision or maneuverability, either, even when meeting tight tolerances.
Tungsten carbide, hardened steel, titanium, Inconel alloys, and even something like Hastelloy – which is a combination of nickel and molybdenum – can all be reliably cut with an EDM tool. These materials are nigh-impossible to cut with great precision while using traditional cutting and machining tools.
6. They Can Create a Unique Finish
Depending on the speed of the cut, it’s true that EDM tools may leave surface defects like craters and pockmarks – mostly when carried out quickly. This can be used as an advantage while adjusting various parameters. For example, cutting slowly at low power reduces the defects and creates a much smoother surface, which even leaves a mirror-like finish.
Operators can adjust as necessary to both improve the finished piece and reduce additional steps. Creating that mirror-like finish on the first go means other tools aren’t needed to achieve the same result. Of course, it depends on the limitations of the product. Because of how EDM machines work, simultaneous finishing is also a possibility – like sandblasting the surface while the original cut is taking place. This speeds up production overall, and can also help generate quality pieces.
Electrical Discharge Machining Offers Better Results
EDM machines shouldn’t be used to cut materials like plastic or plaster, so the technology isn’t ideal for every situation or application. That said, electrical discharge machining offers many benefits over traditional solutions while working with hard materials and metals.
Teams will benefit from unprecedented precision, with the option to make deeper cuts and create sharper edges all while experiencing much less resistance. EDM tools are also incredibly reliable and a lot less prone to errors, which means they can run as much as needed, with minimal intervention, even in an automated “lights out” facility.
At the very least, there’s no reason why machine shops shouldn’t have a few electrical discharge machining tools in the facility or on the shop floor.
Comments (1)
Featured Product
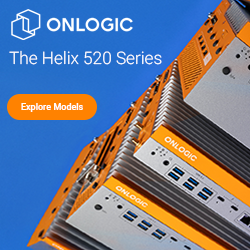