Investing in the UK's injection moulding sector - The case for all-electric machines and robotic integration
Traditionally, our manufacturers have relied on hydraulic-powered injection moulding machines in their operations. However, the industry is now at a crossroads, faced with the imperative to embrace technological advancements for sustainability and cost-effectiveness.
Using Advanced Cooling Techniques to Reduce Cycle Times and Improve Quality in Injection Molding
If parts do not cool down enough or cooling happens unevenly, they can shrink or warp, requiring time-consuming rework processes. Fortunately, numerous ways exist to accelerate cooling time while ensuring it happens effectively.
The Future of Injection Molding Relies on Automation
While demand for injection molding products grows, manufacturers are grappling with persistent challenges, particularly staffing and output.
Sustainability and Plastic Injection Molding in the Automotive Industry
With the ability to use various materials to produce automotive components, car manufacturers will turn to the plastic injection molding industry as the solution.
3D Printing - an Alternative to Injection Moulding?
3D printing technologies have been refined to such an extent that they are truly viable production technologies. Now the conversation among manufacturers is around the most judicious use of 3D printing for production.
Three Ways Autonomous Machine Vision (AMV) Benefits Plastic Injection Moulding
Plastic injection moulding is a difficult application for machine vision. The highly reflective surface of plastics is hard to illuminate, and the fact that the same production line can create items of different colours and shapes is problematic for traditional solutions.
Calculating Injection Molded Plastic Part Shrinkage
When designing any part for injection molding, it is important to consider the shrinkage and contraction rate of the material and the associated geometry of the component. Plastic shrinkage is the dimensional change that occurs in a molded part as it cools after injection.
PRECISION MOLDING & THE INTERNET OF THINGS
While most analysis of the IoT is in respect of its positive influence on manufacturing processes, the growth in the IoT also opens up huge possibilities for micro molding as there is burgeoning demand for a variety of new and innovative micro devices.
In-house Packaging Operations Propels Growth for Tropical Trade & Industries N.V.
New blow-molding equipment and custom bottle designs boost sales by 24 percent in a year for Caribbean syrup and essence manufacturer.
Injection-Molded Plastic Allows More Creativity than Ever Before
Not being limited to metal (or a few standard plastics) opens up a much wider range of design options for engineering and design teams. They can think in more creative ways about complex geometry, performance in harsh environments, shielding considerations etc.
Extending the Life and Improving the Performance of Plastic Injection Molds
Coating mold components like ejector guide elements, cores, lifts and cavities increases the lifespan of molds while reducing maintenance and running costs.
How Colorants Affect Plastic Characteristics
Believe it or not, there is a whole scientific body of knowledge about the ways in which adding color to plastic can affect the behavioral properties of the plastic.
Injection Molding Design & Process Optimization
This approach is superior to standard molding procedures because of the high level of scientific control utilized through upfront Design of Experiments (DoE), flow analysis, process monitoring, and quality control that can quickly detect and correct any process variations.
Hand Loads: Cost Effective Solutions for Complex Plastic Parts
It's important to note that hand loads require extra labor for installation and removal. While this may skew the cost/benefit analysis, it may also be the only way to meet the customers needs.
Voodoo Automates 3D Printing to Take on Injection Molding
Michael Molitch-Hou for Engineering.com: With Project Skywalker, Voodoo Manufacturing was able to automate an important part of its manufacturing process.
Records 1 to 15 of 17
Featured Product
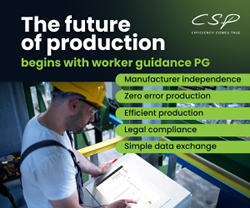
Quality assurance in the manufacturing industry
Efficiency and precision with CSP software. In the highly competitive world of manufacturing, quality assurance is a critical factor for success. CSP offers you state-of-the-art software solutions specifically designed to ensure the highest standards of quality assurance in the manufacturing industry.