Not being limited to metal (or a few standard plastics) opens up a much wider range of design options for engineering and design teams. They can think in more creative ways about complex geometry, performance in harsh environments, shielding considerations etc.
Injection-Molded Plastic Allows More Creativity than Ever Before
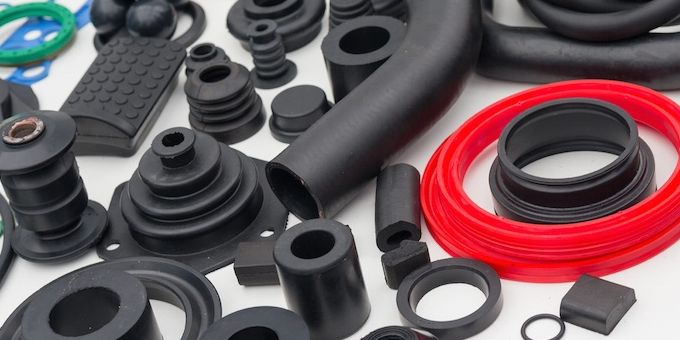
Al Timm | Kaysun
Design teams are always trying to come up with something better—better shapes and designs, better performance, better materials, and most importantly, a better cost. If there's a way to give their product an edge over the competition, the design team will do everything they can to incorporate it into their process and product.
Cost, of course, is a huge factor. After all, there is only so much you can do to reduce costs when you follow Lean practices and/or consistently use the same set of materials, designs and processes. Often it's just a one-percent gain here, a one-percent reduction there.
Creativity and Flexibility Matter
For designers, creativity can help solve several challenges. If a part is designed to be one component instead of several, for example, you can save significant time and costs during production and assembly. However, it's difficult to be creative when you are limited by material choices—especially metal. That's why many of today's manufacturers are exploring metal-to-plastic conversion options.
If I told you switching from metal components to plastic could save you up to 50 percent in operational costs without compromising function or quality—and even improve design choices and options—would you be interested? Of course you'd be! You'd also be skeptical, perhaps thinking something along the lines of “You can’t replace metal with plastic. How about that snow shovel I bought last year? Plastic breaks.”
Well, it’s time to change that mindset.
Benefits of Metal-to-Plastic Conversion
If you aren’t familiar with their incredible functionality, here are some key points to consider when comparing engineered plastics to metal:
- Comparable tensile strength
- Up to 50 percent lighter weight
- Highly repeatable process (less scrap)
- Lower manufacturing costs
- Greater design flexibility
- Increased market stability for material cost
- Lower packaging and shipping costs
- Up to six times longer tool life
- 25 to 50 percent savings in production costs
Maximizing the benefits of engineered plastics in metal-to-plastic conversion is achieved in several ways. Multiple metal parts can be replaced by one injection-molded plastic part, eliminating the need for fasteners and assembly. Colors can also be added to the plastic melt, eliminating the secondary operations of painting. Also, when you compare costs, plastic has a nominal impact on part cost compared to sheet metal.
If you haven’t worked with plastic, this all may sound unbelievable—but it’s true! Plastic parts can be just as tough as metal parts, and meet the same tight tolerances with fewer secondary operations.
With appropriate design, plastic parts can perform just as well as their metal counterparts. In fact, plastics provide greater design flexibility because they can be engineered to have specific physical and chemical characteristics that are better than metal. Plus, there are plenty options to choose from—more than 25,000 engineered materials are available for manufacturing applications. High-performance blends and hybrids can also be custom-designed to meet very specific mechanical, thermal, chemical, electrical, and environmental performance requirements, usually at lower cost than metal parts.
Why Today's Manufacturers Are Making the Switch
As great as these advantages are, metal-to-plastic conversion is still relatively unknown outside the automotive industry, which has zeroed in on plastic components for reducing weight, improving strength, and resisting corrosion. Twenty years ago, thermostat housings and cooling system components were essentially all cast and machined. Today, most of them are injection-molded, polyphenylene sulfide (PPS) components. Plastic components are also used in powertrain, cooling, transmission, steering, fuel, braking, safety and electrical systems as well as for interior and exterior decoration.
What was considered impossible 10 years ago for plastic is becoming commonplace today across a range of industries. Plastic is replacing metal in consumer products, manufacturing and automation equipment, dental and surgical tools, pumping equipment, pneumatics, tractor roofs, pet cage trays, housings (water meters, lawnmowers, power equipment), fuel tanks, heat sinks, water pipes, carts, medical devices, LED lighting systems, packing materials, food processing systems, folding tables, utility pole cross bars, EMS equipment, fasteners and conveyor belt components. Even the wood in wooden pencils is being replaced with thermoplastic because it is more durable and can be produced at lower cost.
Not being limited to metal (or a few standard plastics) opens up a much wider range of design options for engineering and design teams. They can think in more creative ways about complex geometry, performance in harsh environments, shielding considerations, weight and structural limits, thermal management, and product differentiation—both for performance and how the product looks on the shelf. It is much easier to create complex shapes and parts (often of smaller size) using injection molding as well. Plastic allows for uniform thinner-walled parts thanks to its high injection pressure capabilities, replacing the more costly (and heavier) thicker-walled die-cast metal parts. The costly assembly of metal parts can often be replaced by a single injection molded part too, eliminating the need for welded joints between metal parts and also eliminating risks for leakage.
As material suppliers continue to develop high-strength thermoplastics that are increasingly impact-resistant, corrosion-resistant, and heat-resistant, more companies are converting metal components to plastic. Learn more about metal-to-plastic conversion by reading our whitepaper, Metal-to-Plastic Conversion: Revolution the Manufacturing Process.
The content & opinions in this article are the author’s and do not necessarily represent the views of ManufacturingTomorrow
Comments (0)
This post does not have any comments. Be the first to leave a comment below.
Featured Product
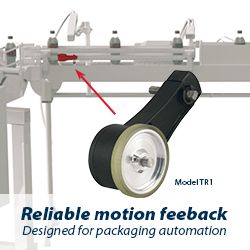