Believe it or not, there is a whole scientific body of knowledge about the ways in which adding color to plastic can affect the behavioral properties of the plastic.
Denny Scher | ICOMold
There are many synthetic polymers available today, each with its own unique properties. Some are more impact-resistant than others, some have more UV resistance, and some bend more rather than break. Anyone starting a custom plastic injection molding project should have initial discussions with their injection molder about material options, in order to choose the most suitable material with the properties needed for the function of the parts.
One aspect of polymer characteristics that doesn’t always get the consideration it deserves is the addition of colorant. Believe it or not, there is a whole scientific body of knowledge about the ways in which adding color to plastic can affect the behavioral properties of the plastic. This paper takes a high-level look at some of the different, and surprising, ways colorants can have an effect on plastics.
Compatibility
When developing a colorant package for any polymer, it’s very important to consider the compatibility between the chemistry of the polymer and the chemistry of the colorant. Some of the compounds in colorants can break down the chemistry of the polymer and weaken its original properties, like impact-resistance. The high heat used in injection molding can also influence the degree to which the colorant affects the polymer. The colorant itself must also be capable of surviving the high processing temperature. And, a certain colorant may affect one polymer differently than it does another based on temperature, despite being chemically compatible. It’s also worth noting that the interaction between a polymer and a colorant can also be affected by other additives. For example, a polycarbonate otherwise unaffected by a colorant may have a different reaction to it when a flame retardant is added to the PC.
Amount of Colorant
The property retention of the polymer is also a function of the amount of colorant incorporated into it. If you think of colorants as contaminants, the more you add, the more negative impact it can have on the plastic. Adding 1-2% of a colorant is usually harmless, as long as the compatibility issues mentioned above don’t come into play. As colorant levels rise, the greater the chance that the plastic properties will shift.
Different Colors, Different Properties
“Molecular weight” and “crystallinity” are factors in the equation, but in layman’s terms the bottom line is that different colors can affect a polymer in different ways. For example, transparent colors can be made with dyes which are potentially less impactful on the polymer structure than the pigments used in opaque colors. Pigments are made of particles, and the size of those particles can impact the performance of the material. Molding the same part in different colors can actually result in differing part dimensions, which can be important if very tight tolerances are critical.
Method of Colorant Incorporation
There are several different methods of coloring plastics, including masterbatch, compounding, surface coating and dry blending. They each have their advantages and disadvantages and vary in cost, color consistency and other factors. The coloring method used can influence the mechanical properties of the plastic. For example, in the masterbatch method, pellets of natural color are blended with a “masterbatch” of pellets with a high pigment content. Since most polymers do not tend to mix well with other polymers, care must be taken to ensure material compatibility, or the blend can cause problems.
In summary, the effect of colorants on injection molded plastic parts is more complex than we think, and it’s not usually at the top of the list of considerations in planning an injection molding project. But it is important and needs to be addressed at the material selection stage.
About Denny Scher
Denny Scher is the Marketing Manager for ICO Mold, a U.S.-based custom plastic injection molding and CNC machining company. He has written numerous technical articles for the automotive aftermarket and plastics industries. In his spare time, Denny enjoys playing and teaching guitar.
The content & opinions in this article are the author’s and do not necessarily represent the views of ManufacturingTomorrow
Comments (1)
Featured Product
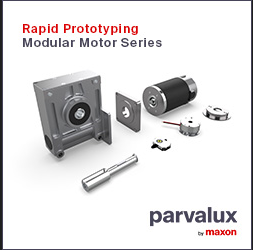