The Potential of Polymer 3D Printing - Exploring Advanced Manufacturing Processes and Bearing Design
Metal Additive Manufacturing: The Cheaper the Better, asks IDTechEx
Successful use of Carbon-composite Windform® XT 2.0 and professional 3D printing in the construction of 1P PocketQubes flight-ready
When Should You Use 3D Printing for Production?
MICRO MOLDING FOR MICRO-ELECTRONICS
Smart Manufacturing Control
World's first 3D printed FRP footbridge paves way for circular composites
Vertical Integration - The Key to Micro Molding Success
What is Cast Urethane Manufacturing?
Micro Molding and Micro Optics
Smith College Team From Massachusetts Wins CoVent-19 Challenge to Design New Ventilator for Developing World
Multi Property Optimization for Injection Moulding to Maintain Safety and Reduce Manufacturing Costs
The New Normal for Global Manufacturing
3D modelling technique for fast-track face shield production
PRECISION MOLDING & THE INTERNET OF THINGS
Records 166 to 180 of 755
First | Previous | Next | Last
Additive & 3D Printing - Featured Product
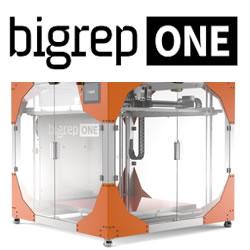