Metal Additive Manufacturing: The Cheaper the Better, asks IDTechEx
Metal additive manufacturing has seen many trends over recent years including pushing the (build) envelope & deposition rate to higher levels, broadening the materials portfolio, and expanding into new markets. One trend that cannot be overlooked is the number of product launches for low-cost "desktop" variants; the question is will they be successful?
It is well-known for polymer 3D printing that the hobbyist market, which, although popular and great for engagement, is not where the value lies. The majority of the market value is and will be based in industrial applications. Metal additive manufacturing currently services high-value industries, most of the printers sold are powder bed fusion and can cost over $1m with expensive powder feedstocks. The industry is forecast to have a fall resulting from COVID-19 before rising to significant levels, for more information see the comprehensive technical market report: "Metal Additive Manufacturing 2020-2030".
The high price-tag for current metal printers has kept it in the realms of high-value industries such as aerospace & defense and medical. Powder bed fusion processes are gaining traction in other sectors, such as energy, but require time to find the economically viable use-cases. There are a large number of alternative printer processes emerging, including directed energy deposition (DED), metal binder jetting, material jetting, and more. The report highlights all the main players and benchmarks the different processes against each other, allowing the gaps in the market to be observed.
One recent trend is the release of "desktop" or cheap/affordable metal printers. Here we are not talking about systems costing around $0.5m and targeting small-to-large part production but rather those at ca. $100k or below. These small printers are designed to make this technology more accessible and ideal for research, prototyping, and small replacement parts.
There are numerous players entering this field with different processes. The bound metal approaches of Markforged and Desktop Metal grab most of the headlines, although there are others extruding pellets (rather than filaments) and Rapidia with a "water bound" approach. Then beyond that, there are players like One Click Metal (a TRUMPF spin-off) making low-cost powder bed fusion machines and the likes of Meltio and InssTek making directed energy deposition units utilizing wire and powder feedstocks, respectively. Some companies have their whole business model around these low-cost printers whereas others have them as more as a secondary side project, the issue comes with the economics.
To make these printers a success, large annual sales volumes are needed which means a far greater adoption than has previously been observed. The follow-on sales from materials will not be as significant and the "simple" designs will result in less servicing, installation, and training fees. The counterpoints are that there will be software services and a replacement market which could be beneficial with a large installed base.
There are also printer limitations that are quick to be overlooked. For bound metal processes, this includes necessary debinding steps (which brings solvent considerations, cost implications, and part thickness limitations) and consolidation in a sintering furnace (bringing impact on size, time, and cost). The same is true for other processes and although they are not deal-breakers (and there are constant innovations progressing this), it does mean they are not the small, cheap, "plug-and-play" printers initially perceived.
Then there is the important question of what the adoption will be like. This is unchartered territory and although the products are at an attractive price point, and there are good early signs, the market potential has many barriers to be truly realized. The competitive landscape is heating up, the complicated legal history between Markforged and Desktop Metal is well documented and given both have significant funding and valuations there is clear confidence in the potential. It should be noted that both players have other offerings that could prove more lucrative in the longer-term.
IDTechEx has released a detailed technical report on "Metal Additive Manufacturing 2020-2030". This report goes into tremendous depth through deep technical knowledge and an extensive number of primary interviews. Granular market forecasts, detailed company profiles, technology benchmarking, and material portfolio assessments are all included within this report.
Beyond the bound metal printers, Markforged are major players in 3D printing of continuous fiber composites. Desktop Metal also entered this field in late 2019 with their Fiber printer and there are many more new and established players developing this technology. This includes a wide range of fiber integration, material choices, and design opportunities. IDTechEx has a market report dedicated to this industry, "3D Printing Composites 2020-2030: Technology and Market Analysis".
For more information on this report, please visit www.IDTechEx.com/MetalAM or for the full portfolio of Electric Vehicles research available from IDTechEx please visit www.IDTechEx.com/research/3D.
IDTechEx guides your strategic business decisions through its Research, Consultancy and Event products, helping you profit from emerging technologies. For more information on IDTechEx Research and Consultancy, contact research@IDTechEx.com or visit www.IDTechEx.com.
Comments (0)
This post does not have any comments. Be the first to leave a comment below.
Featured Product
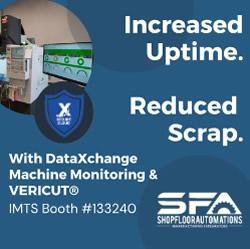