Supply chain uncertainty gives workers a chance to shine
5 Promising Innovations in Metal Finishing Techniques
How to Overcome Common Manufacturing Storage Challenges
CNC Data Transfer Methods That a CNC User Must Know
Lessons to Learn from Intel's $20 Billion Manufacturing Investment
Rising Demand for EVs Will Disrupt Auto Manufacturing
Tips to Help Manufacturers Address the 2021 Labor Shortage
Here's How to Improve Quality Control in CNC Machining
How VR can Ensure Manufacturing Safety
Using AI to Enforce Safety Compliance in Manufacturing
Why Laser Technology Is a Good Automation Tool for Traceability
Three Manufacturing Tips to Strengthen America's Competitiveness & Maintain National Security
How will the Food Manufacturing industry bounce back in 2021?
Model-based enterprise as a trigger to Digital Transformation
Designing Zero Defect Manufacturing Systems Post-Pandemic
Records 121 to 135 of 384
First | Previous | Next | Last
Supply Chain - Featured Product
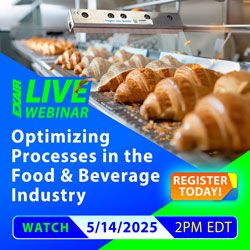