CNC Data Transfer Methods That a CNC User Must Know
Computer Number Control or CNC machines allow users to create a part or equipment out of a block of metal or plastic by continuously removing pieces of metal in a pre-determined manner. It is also known as a subtractive manufacturing process.
Gone are the days when a person oversaw and performed every task associated with manufacturing machine parts. With CNC machines, software that has already been programmed with the required design can govern the movement of the tools. The program can cover different types of machinery and can also cover a wide range of tools.
Data Transfer Methods That a CNC User Must Know
The data stored in the CNC machine gains significant importance as it is the data that lets users complete the project. If you repeatedly make the same design, storing the program in a safe external device becomes even more important.
Data transfer is a process that takes place regularly in the life of a CNC user. While a CNC user might employ various methods for data transfer, they can either be classified based on the type of data being transferred or the method of data transfer employed.
Methods Depending on the Data Being Transferred
A CNC machine uses programs that tell the machine where to use a tool, how to use and how far to drill, etc. All of this information is important and should be stored properly.
CNC System Data
Every CNC machine has data about its system functionalities. This data will change from one machine manufacturer to another significantly. There may even be small changes between the system data for machines made by the same manufacturer.
Certain parameters, such as backlash, pitch error compensation, etc., are machine-specific. Every CNC user must back up this data in external storage space. Doing so ensures that it is easier to get the CNC machine up and running in the unfortunate incident of a machine failure.
Fixture Offsets
A CNC machine of any kind, be it a CNC turning center or a CNC lathe, needs to have well-defined zero assignment values. These values help the machine move the required parts to the appropriate position to chipping away from the raw block.
Every time a job is run on the CNC machine, it is important to use the same fixture offset values, especially if the same part is being manufactured repeatedly.
G10 commands are an excellent way to set the fixture offset values correctly before running the CNC program. These commands are typically present at the start of the CNC program.
You can transfer the fixture offset settings into a CNC program file and run the file every time you initialize the machine.
Tool Offsets
Tool offsets are also G10 commands similar to the fixture offsets. The tool offsets help the machine identify the center of the tool so that the machine runs along the intended programmed line.
The tool offsets depend on the length and the diameter of the tool. Therefore, if the tools are changed, the tool offsets need to be reset to match the new tools.
Transferring the tool offset data from the machine is often done to confirm that all the offsets are set properly and that there aren't any unwanted variations.
Custom Macro Variables
Custom macro variables that common permanent variables that can be used to set values for various accessories. They can also be used as system constants or timers.
Creating a backup file of the custom macro variables present in the machine ensures that you do not accidentally end up using any previously defined variables. The data file that defines the custom macro variables contains a series of G10 commands.
Modes Employed for Transfering the Data
Depending on the CNC machine and its features, there are various ways of transferring the data to and from the CNC machine. While punched tape and floppy disks used to be the go-to methods for data transfer, they are now replaced by standard V24, RS232, or RS485 serial interfaces.
A wired connection to a storage device or another computer is also often used for data transfer. Newer CNC machines can also use a wireless connection to transfer data.
If the CNC machine has a small memory that is inadequate for storing the program, the program is stored in a computer connected to the CNC machine. The program is then transferred in smaller blocks to the CNC machine. This process is also known as Distributed Numeric Control.
Key Takeaways
The various system data associated with the CNC machine are an integral part of the CNC process. Without proper input for the system data and offsets, the machine fails to reproduce the design that was in the program.
Every CNC user is well-versed in how to transfer the data mentioned above using any of the techniques mentioned above and knows about the latest storage methods. The choice of the technique might depend on the features of the machine. It is also important to know when to load certain data types and when to recheck the data.
About the Author:
Vincent Hua is the Marketing Manager at TSINFA. He is passionate about helping people understand high-end and complex manufacturing processes. Besides writing and contributing his insights, Vincent is very keen on technological innovation that helps build highly precise and stable CNC Machinery.
Comments (0)
This post does not have any comments. Be the first to leave a comment below.
Featured Product
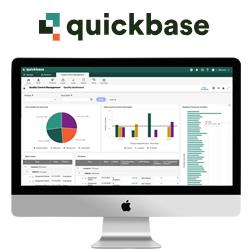