Reducing Parts Costs as Production Scales Up
ManufacturingTomorrow - Special Tradeshow Coverage
MODEX 2018
PlastiComp Part of Team Working to Accelerate Development of Affordable Carbon Fiber Composites
The Many Uses of Bellows
Industrial PCs: Addressing the Top Five Challenges on the Factory Floor
Kerk Lead Screw Allows RPT Motion to Create Quick and Cost-Effective Case Packer
When Should You Re-Manufacture or Refurbish Equipment?
Robot welding: More efficiency for programming and equipment fabrication
3D printing revives hard-to-find Porsche Classic parts
Manufacturing Transportation and Logistics 101
Injection Molding Design & Process Optimization
Magic 2018 Preview: Moving Into The Future Of Fashion Production And Reimagining Retail
Hand Loads: Cost Effective Solutions for Complex Plastic Parts
IDC Manufacturing Insights
Smart Factories Need Space and Time Anchors
Records 496 to 510 of 826
First | Previous | Next | Last
Supply Chain - Featured Product
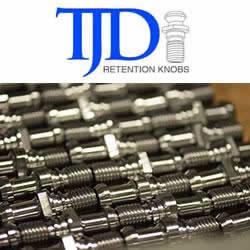