In most cases, re-manufactured hardware is better because its closer to new. That doesnt mean refurbished hardware is bad, just that you should remain aware of the differences.
When Should You Re-Manufacture or Refurbish Equipment?
Megan Ray Nichols | Schooled By Science
There are many ways to cut costs or boost financial efficiency in construction, manufacturing and development. One often-overlooked way is using or deploying tools and hardware your company doesn’t own.
It wasn’t always an option, but today, companies have many viable choices outside of buying brand-new equipment and hardware. You can lease or rent equipment, which opens up the possibility to choose and deploy hardware on a project-by-project basis. You can also buy used, re-manufactured or refurbished equipment.
There is another route, of course. Rather than replace or throw out your old equipment, you could update it to meet current standards and efficiency demands. Surely, you’ve heard of refurbished and re-manufactured products or goods before, right?
For some, this can seem necessary because machine tools and hardware are vital and costly components of your business. Tools, hardware and machinery can represent capital investments, which you don’t want to lose. Boosting or increasing their viability is an alluring scenario.
Refurbish vs. Re-Manufacture
Before we go on, yes, there is a difference between re-manufactured and refurbished. Refurbished means someone returned an item to the manufacturer or vendor for an unknown reason, and the manufacturer repaired it, tested it for defects and put it back on the market.
Re-manufacturing is similar, though it involves the replacement of worn or obsolete components and or modules. The product as a whole undergoes a more rigorous testing and validation process and may even be further improved for adherence to updated specifications or regulations.
Hydraulic re-manufacturing is an excellent example, because it involves complex components or machinery where everything needs to be operating at full efficiency. You would choose the re-manufactured route over refurbishment when you need to be sure the systems are in perfect working order.
In most cases, re-manufactured hardware is better because it’s closer to new. That doesn’t mean refurbished hardware is bad, just that you should remain aware of the differences.
Now that’s out of the way, let’s explore the idea of updating your old hardware or equipment.
When to Re-Manufacture or Refurbish
When done at the right time, by the right professionals, with the right equipment, refurbishment and re-manufacturing can net a massive savings. The most important factor in taking advantage of this is knowing when the opportune moment is. If you do it too soon, you sacrifice precious operating hours and money. Do it too late, and you must go without the necessary equipment and hardware while it’s out for repairs, and possibly even pay higher costs for a quick turnaround.
There are three elements to consider when deciding whether the time is right to retrofit your equipment:
-
Type of machine or hardware in question
-
The size of your fleet, including backup hardware
-
The age and condition of your machine(s)
Why the Type of Hardware Matters
Compact equipment — such as backhoe loaders, augers and trenchers — hold a remarkably strong resale value. That makes it almost silly to consider refurbished owned equipment. You can easily find someone willing to buy your old gear, as well as someone selling theirs. In the current market, you can also buy a new one for a decent price. Therefore, compact machinery is not a good candidate for refurbishment or re-manufacturing.
Mid-sized equipment or larger, however, most certainly is. Some examples include articulated haulers, wheel loaders, excavators and larger machines or furnaces. The internals or components of a machine may be costly, but less so than buying new equipment outright. Furthermore, you can still get a decent amount of life out of the larger equipment after replacing a few parts or systems.
What About Fleet Size?
Since retrofitting can take anywhere from 60 to 180 days — depending on the machines and components that need replacement — you’ll want a suitable alternative in the meantime. If you’re a smaller player in the market and only have a handful of machines with little to no backup, refurbishment might be out of the question just because of the time it takes. Don’t rule it out, however. Do what you can to find ways to cope while your equipment is out for repairs, because the cost savings are definitely worth it.
That said, you can see why fleet size and backup hardware is an important part of re-manufactured and refurbished systems processes. If you don’t have any, you’re going to be without equipment for quite a while.
What Does Age Have to Do With It?
Sometimes, the industry or technology in question has advanced considerably in the time you’ve owned and used your existing hardware. In this scenario, when equipment dies or malfunctions, it’s beneficial to completely update the hardware. This is true pertaining to regulations and emissions, new features, automation and much more. Just remember to calculate both maintenance downtime and employee training into your total replacement timeframe.
Refurbishing or re-manufacturing your equipment is beneficial if you don’t have the money to upgrade, but sometimes, there’s no reason not to.
Furthermore, the age and condition of the hardware in question matters. Wheel loaders, for example, are generally reliable up to the 12,000-hour range. From about 12,000 to 15,000 hours, they tend to experience higher instances of breakdowns and malfunctions, putting them at the “golden age” for refurbishment.
So, at right around 12,000 hours, standard practice would be to have the machine inspected and appraised. If it turns out the hardware is in good condition, you can push the operational hours further, since you know loaders tend to be reliable after up to 15,000 hours of use. Retrofitting that wheel loader after about 10,000 hours of use, for instance, would be a huge waste.
Save Money by Retrofitting Hardware
Yes, you can ultimately save a lot of money by refurbished or re-manufacturing hardware, but it also depends on the machine or systems in question. If they have a lot of life still left in them and you retrofit early, you’re going to be wasting operational hours, costs and much more.
You also want to be sure you have the appropriate fleet backups handy when you send your equipment and gear off for servicing. It’s not an instant process, and takes times for repairs and maintenance, so you’ll need an alternative in the meantime. Otherwise, you risk shutting down your plant or locations until you have your hardware back in possession.
Follow the guidelines set forth here, however, and you should come out on top.
The content & opinions in this article are the author’s and do not necessarily represent the views of ManufacturingTomorrow
Comments (0)
This post does not have any comments. Be the first to leave a comment below.
Featured Product
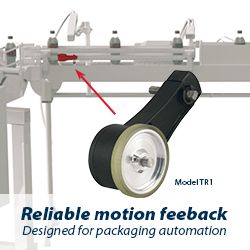