Beyond the Hype: What's Next for Industrial 3D Printing
Oerlikon expands additive manufacturing R&D and production capacity in the US
Stratasys launches new rapid prototyping Engineering-Grade 3D Printing Solution: The F123 Series
Google Ventures, BMW, Lowe's Invest in Desktop Metal
MIT Builds Invisible Fish Grabbing Robot
The 9 unit Winbo 3D printer is an all-in-one micro factory
Adidas reveals plans for 3D printing 'Speedfactory'
ASU site of largest academic additive manufacturing center in the southwest US
The 3D Printers of CES
3D graphene: MIT scientists develop super-light, super-strong structure
CES 2017 - MarkForged 3D prints metal
3D printer builds a cube from a vat of goo … using a phone screen
Dubai Govt, US startup to team up for 3D printing
Using 3D Printing, Lithography & Soft Robotics: New Prosthetic Hands Made for $50 at Cornell
Spanish City Installs 3D-Printed Bridge
Records 301 to 315 of 449
First | Previous | Next | Last
Additive & 3D Printing - Featured Product
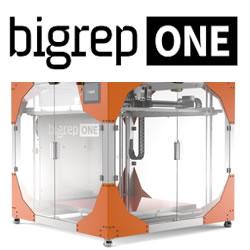