Intel Forecasts 2017 Industrial IoT Trends
EtherCAT Soft Motion Control Auto-Configuration
Seven Career Paths Opening With the Industrial IoT
Desktop Factories: A 'Moving' Look at 3D Printing
Using the Endurance L-Cheapo 5.6 W (5600 mW) Semiconductor (Diode) Laser Operation
US Manufacturers Too Slow to Adopt Industry 4.0: BCG Study
The Latest and Greatest of 3D Manufacturing
Keys To Developing A Successful Product Prototype
The Rise and Fall of the Everyman Tycoon
IIoT's new business models
Sanitary Conveyor System from Dorner Helps Wisconsin Cheese Packer Improve Ergonomics and Packaging Efficiencies
Robots won't kill the workforce. They'll save the global economy.
How to Choose a Controller for Motor Applications
The Pursuit of the Perfect Part
Researchers 3D print working drone with embedded electronics
Records 2536 to 2550 of 2980
First | Previous | Next | Last
Featured Product
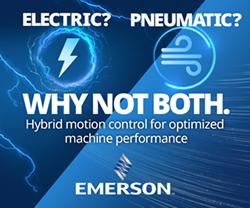