AIA Announces The Vision Show Startup Competition Finalists and Judges
Sensai Modernizes Manufacturing Operations With AI; Launches US Pilot Program
Russell Compact Sieve® skyrockets efficiency at New Balance additive manufacturing center
Siemens invests in new 3D-printing facility in UK
New Story and ICON Unveil First Permitted 3D-Printed Home Created for the Developing World
Swinburne to establish world first Industry 4.0 Testlab
buildPl8 Manufacturing Launches Cloud Based 3d Printing Factory
How Executives Around The World View Industry 4.0
America Makes, Laser Institute of America, Fab Foundation and Fab Lab Hub Collaborate in 2018 Digital Fabrication Conference
Combining augmented reality, 3D printing and a robotic arm to prototype in real time
Organic molecules enable 3D printing of nanoscale metal structures
Shanghai instals 3D bus shelters
3D printing revives hard-to-find Porsche Classic parts
Magic 2018 Preview: Moving Into The Future Of Fashion Production And Reimagining Retail
Startup Wants to Connect Thousands of 3D-printers in a Blockchain-based Network Hub
Records 781 to 795 of 1242
First | Previous | Next | Last
Featured Product
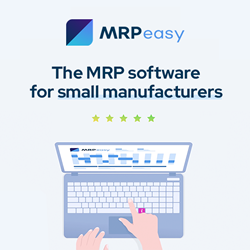