Sensai Modernizes Manufacturing Operations With AI; Launches US Pilot Program
Sensai, an augmented productivity platform for manufacturing operations, today announced the launch of its pilot program in the United States. Sensai increases throughput and decreases downtime with an innovative AI technology that enables manufacturing operations teams to effectively monitor machinery, accurately diagnose problems before they happen and quickly implement solutions.
Currently, manufacturing operations solutions are siloed and offer limited collaboration capabilities, leaving plant, maintenance and operations managers in the dark about the true status of production. Through the empowerment of people and digital transformation of current assets into a modern cloud-based collaboration hub, Sensai elevates and presents valuable information from every asset and person in the production process in a simple and efficient manner. Manufacturing operations benefit from increased profitability through identification and reduction of downtime, making processes run even faster and more efficient.
“The possibility for momentous change within manufacturing operations through digital transformation is here and now,” said Porfirio Lima, CEO of Sensai. “As an augmented productivity platform, Sensai integrates seamlessly into old or new machinery and instantly maximizes uptime and productivity by harnessing the power of real time data, analytics and predictive AI. Armed with this information, every person involved - from the shop floor to the top floor - has the power to make better and faster decisions to increase productivity. Sensai is a true digital partner for the operations and maintenance team as the manufacturing industry takes the next step in digital transformation.”
How Sensai Works
Sensai’s augmented productivity platform is a holistic enterprise system that combines human- and tech-based solutions, connecting, informing and using data-driven intelligence to cut costs by minimizing downtime and limiting defects. By simply installing a set of non-invasive wireless sensors that interconnect through a smart mesh network of gateways, Sensai collects data through its IIoT Hub, gateways and sensors, and instantly sends it to the cloud or an on-premise location to be processed and secured. As a result, operations teams are always aware of production status, machinery requirements and needs with fast and easy communication through user-friendly dashboards, mobile applications and cloud-based connectivity to machinery.
The Sensai Difference
Sensai’s differentiator is that it provides a full state of awareness, not only of the current status, but also of the future conditions of the people, assets and processes on the manufacturing floor. Sensai will learn a businesses’ process and systems with coaching from machine operators, process and maintenance engineers. It will then make recommendations based on repeating patterns that were not previously detected. Sensai does this by assessing the team’s experiences and historical data from the knowledge base and cross checking patterns of previous failures against a real-time feed. With this information, Sensai provides recommendations to avoid costly downtime and production shutdowns. Sensai is a true digital peer connecting variables in ways that are not humanly possible to process at the speed required on a today’s modern plant floor.
About the Pilot Program
Participation in Sensai’s pilot program is possible now for interested manufacturers. Already incorporated throughout Metalsa, a leading global manufacturer of automotive structural components, Sensai is set to digitally disrupt the manufacturing industry through AI, including those in automotive, heavy metal and stamping, construction materials, consumer goods and more. The pilot program process includes five stages:
- Assessment: Cultural fit, technological capability, knowledge availability and expected business outcomes are evaluated. Sensai gets a 360-degree view of the gaps to fill and advises how to add value in a short period of time.
- Instrumentation: Prioritizing on the expected outcomes, Sensai maps out how to successfully monitor the shop floor based on wireless and non-invasive technology.
- Implementation: The operations team and all stakeholders are informed, prepared and trained to maximize the benefits from the platform.
- Evaluation: After the three-month period, results of the pilot program are presented and compared to the initial business case prepared in the assessment to showcase the fulfillment of the expected outcomes.
- Rollout: After the successful deployment of the pilot, the Sensai team looks into the next five to 10 assets that are of priority and repeats the process.
“Sensai is not a cumbersome and bulky solution that will drain budgets, take years to implement, and even more years to see ROI. It is quick to implement and only grows more intelligent and valuable as it learns a business’ processes and systems. I cannot be more excited about Sensai’s ability to augment human potential through technology,” said Lima.
If you are interested in participating in the pilot program or for more general information, please visit www.sensai.net or email hello@sensai.net.
About Sensai
Founded in 2017, Sensai is headquartered in Monterrey, Mexico and privately funded by Metalsa, a leading global manufacturer of automotive structural components. Sensai is an augmented productivity platform for manufacturing operations that increases throughput and decreases downtime with an innovative AI technology. Sensai enables manufacturing operations teams to effectively monitor machinery, accurately diagnose problems before they happen and quickly implement solutions. The company’s goal is to augment the potential for humans in the world through technology. Learn more at: www.sensai.net
Comments (0)
This post does not have any comments. Be the first to leave a comment below.
Featured Product
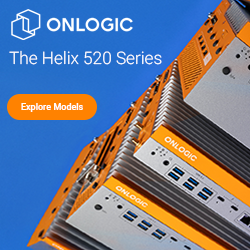