Organic molecules enable 3D printing of nanoscale metal structures
The Engineer: According to a study published in Nature Communications the process, once scaled up, could be used in a wide variety of applications, from building tiny medical implants and 3D logic circuits on computer chips to engineering ultra-lightweight aircraft components. It also opens the door to the creation of a new class of materials with unusual properties that are based on their internal structure.
Nanoscale 3D printing uses a high-precision laser to strike the liquid in specific locations of the material with two photons. Whilst this provides enough energy to harden liquid polymers into solids, it doesn’t provide enough to fuse metal.
“Metals don’t respond to light in the same way as the polymer resins that we use to manufacture structures at the nanoscale,” said Caltech materials scientist Professor Julia Greer. “There’s a chemical reaction that gets triggered when light interacts with a polymer that enables it to harden and then form into a particular shape. In a metal, this process is fundamentally impossible.”
Greer’s graduate student Andrey Vyatskikh came up with a solution that uses organic ligands – molecules that bond to metal – to create a resin containing mostly polymer, but which carries along with it metal that can be printed, like a scaffold.
The team bonded together nickel and organic molecules to create a liquid, designed a structure using computer software, and then built this structure by zapping the liquid with a two-photon laser. Full Article:
Comments (0)
This post does not have any comments. Be the first to leave a comment below.
Featured Product
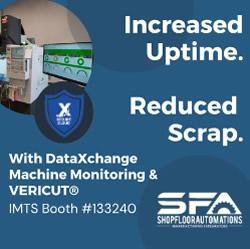