ABB survey reveals unplanned downtime costs $103,000 per hour
Data Guys Versus Production Pros - Who is the Best Person to Train AI Programs for Defect Detection?
What is Augmented Reality in the Manufacturing Industry?
VR Welding and the Future of Metal Fabrication
Giving Second Life to Legacy Systems Through the Industrial Internet of Things
Automation Alley announces new year-long format for Integr8 event
Why Manufacturers Should Leverage Hyperscaler Ecosystems to Accelerate Transformation
Why Prefab Shops Should Digitize Their Workflows & 5 Entry Points
Automotive Assembly Contract Manufacturer Supports Rapid Growth with MRP Software
EU Automation publishes new guide: How to Get Robotics Right - Avoiding the Common Costly Mistakes of Automation Adoption
Ergonomic welding-a contradiction in terms?
What Is MES & Why Should Manufacturers Invest In It?
Thermal Imaging Technology in Lithium-ion Battery Manufacturing
Optical Component Manufacturing - a Lesson in Timing, Trust, Partnership, & Experience
Mastering Configurable BOM Complexity
Records 346 to 360 of 1700
First | Previous | Next | Last
Automation & IIoT - Featured Product
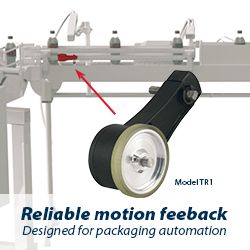