Due to the fact that manufacturing and IT systems have historically developed in parallel, they cannot communicate by default, which forces companies to struggle with compatibility issues when performing digital transformation.
Giving Second Life to Legacy Systems Through the Industrial Internet of Things
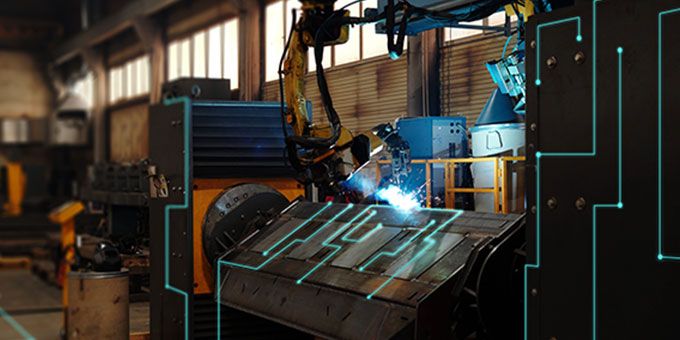
Ms. Julia Mitchell, Business Operations Manager | Professional Software Associates Inc. (PSA)
The 3rd Industrial Revolution has left a rich legacy of highly automated industrial machinery that forms the basis of any significant production. However, today digital has taken a dominant position, and many factories are puzzled about what to do with all this "wealth"? Due to the fact that manufacturing and IT systems have historically developed in parallel, they cannot communicate by default, which forces companies to struggle with compatibility issues when performing digital transformation. As a result of these struggles, integration costs in such cases might be up to 50% of the total cost of enterprise IoT solutions. In the wrong hands, once prosperous factories become a burden that only prevents the transition of production to digital rails. Thus, is it really worth it?
Why Upgrade Legacy Production Systems with the Industrial Internet of Things?
For now, any production that strives for digital transformation utilizes the Industrial Internet of Things. In each specific case, it needs to be addressed if it is possible and advisable to breathe life into the legacy systems, or if it would be much more beneficial to build the cutting-edge IoT production network from scratch. Why should we lean towards the first embodiment? Firstly, the existing manufacturing machines and controllers are powerful enough to assume some of the functions of the IoT ecosystem. Secondly, the existing SCADA systems that control the production processes collect the data by default. This data might be relevant for the Industrial Internet of Things. For instance, the data on temperature or voltage surges within equipment components collected by SCADA might be used for building IoT predictive maintenance algorithms. By adding one essential component – namely, an Internet connection – legacy manufacturing systems would gain visibility, predictability, and flexibility, which completely satisfies smart factory goals.
Thus, the upgraded production system can safely be called the new smart system, since IoT implementation advances not only assets but the ways of their control and maintenance, as well as the approach for production management. After the existing systems' meticulous analysis, it’s possible to build a reliable and cost-effective IoT-enabled ecosystem on its basis. For the most part, it becomes more profitable than building a parallel IoT infrastructure or waiting for the end of the system life cycle.
What Slows Down Traditional Production Systems to Become a Part of the Industrial Internet of Things?
For the legacy production control system to become a part of the Industrial Internet of Things, it’s critical to provide the following features:
-
Continuous multiple data collection
-
Reliable connectivity
-
Cloud connection
-
Real-time operations through the internet
-
Remote control
All these features should be implemented under the conditions of use to contribute to efficient analytics and precise results. That is, the data should be clean and relevant, connectivity should be stable in every area, and bandwidth should be enough to ensure a seamless data transition to the cloud.
The traditional production control is based on RTUs, VFDs, PLCs, and other components that can be considerably powerful but not advanced enough to support the features mentioned above. They all form an integrated infrastructure in which updates should be performed comprehensively starting from organizing the production network. However, this challenge is not as complicated and costly as it may seem if approached hierarchically:
-
Advanced analytics for business planning level
-
Cloud application for control level
-
Advanced connectivity for IoT automation solutions
From Legacy SCADA to Advanced IoT Management & Control
The question of how to comprehensively upgrade production to IoT generally starts with how to deal with SCADA systems that are already responsible for production control. Since SCADA performs data collection, monitoring, management, and report generation, it would be impractical to ignore it and create a parallel IoT-based infrastructure from scratch. The functions of these two systems are largely the same, which brings the following options for their interaction:
-
Integrate IoT components into SCADA. Leaving control functions behind SCADA, smart devices can collect the missing data to provide a more complete picture of production to SCADA. This may also require a power control system to optimize consumption.
-
Integrate SCADA into an IoT management platform. This opens up access for the SCADA-collected data to the cloud and, therefore, advanced analytics. This requires the integration of intermediate devices, such as switches and gateways. In general, IoT platforms may include SCADA, ERP, OPC, and lots of other systems providing comprehensive business management.
The optimal approach can be found in the middle. IoT sensors might be utilized to measure parameters that are not covered by SCADA to gain a complete view of the production processes. For instance, the factory can monitor the flow rate in the pipeline in addition to the pressure. In such a model, the Industrial Internet of Things and SCADA jointly provide the data, SCADA notifies of issues and initiates control measures while IoT getaways help the essential data reach the cloud for the advanced analytics being performed. However, every step is associated with challenges.
Extending Scalability for Industrial Internet of Things
The capacity of legacy systems is insufficient to promptly transfer the data from every sensor to the central database. And it’s especially problematic for them to analyze the data and send results back to the edge. Legacy Database Management Systems (DBMSs) simply can’t ensure control for big amounts of data at the edge and the cloud deployment, as well as they can’t respond to the growth of the connected devices. This requires the data to be aggregated at the edge – closer to the place they are collected. Therefore, the first requirement for legacy systems to get updated is to organize a robust edge infrastructure to distribute the loads. It provides the system with additional flexibility and transmittance as well.
Compatibility Issues for Field Devices
When it comes to primitive machines, the only opportunity for getting them online is to equip them with IoT sensors or RFID tags in adherence to the request and conditions of use. Facing advanced systems like PLCs, we need to transform the existing machine outputs into a modern interface for connecting to the cloud, which can be solved via intermediate (edge) devices that support both legacy and modern protocols. As a transition standard, you can use, for example, RS-232 or RS-485, since most production machines support it. The other reliable solution is to utilize OPC architecture created especially for industrial applications and M2M communications. MQTT with SSL/TLS protocols also stay on top for industrial connectivity, since they provide reliable and secure connection to cloud, edge devices, and IoT gateways.
The crucial point here is to build optimized architecture. For instance, installing an IoT gateway on every machine provides fast and reliable data transport, but is an extremely costly solution. It would be better to install a transmitter that streams data to a central IoT gateway, which then transmits it to the cloud.
Connectivity Issues of the Industrial Internet of Things
The deployment of legacy systems does not imply the need for an Internet connection. Therefore, the existing infrastructures need to be updated to communicate in hard-to-reach places, distant areas, or premises with lots of walls. The first option here is the possibility of deploying a wireless mesh network, for example, via the BLE or Zigbee standard. This works successfully even on factory floors with high levels of electrical noise. Secondly, the shift of significant computing power from the cloud to the edge might help. When the data is processed closer to the source of its collection, operations are performed faster and more accurately. This is especially important for old systems, because of the low bandwidth we mentioned above.
One more thing that can’t be omitted is cybersecurity concerns. Since legacy systems are vulnerable by default, IoT must take all the measures required to protect SCADA-controlled assets, such as network segmentation, regular updates, and access control.
The Imperfection of Hardware Components – How to Increase Performance
Upgrades for the electronics of the production equipment are not the most common but still, a useful approach when it needs to increase performance and support a wide range of IoT functionality, including AI. Modular architectures provide easier updates through simple substitutability between system components. For example, COM Express has the potential for Industrial Internet of Things and AI applications supporting outdated interfaces, such as VGA or PCI, and allowing for the integration of modern 7th-generation Intel Core processors. Overall, updating of hardware components may allow for 10x performance acceleration, RAM, and flash memory extension, which might be essential for particular IIoT applications.
Legacy Systems for Industrial Internet of Things: Final Thoughts
-
Industrial Internet of Things extends the capabilities of your legacy systems, improving process visibility, and enabling a connected environment to achieve smart factory goals.
-
The major point when upgrading the legacy production systems is to build the infrastructure optimized under conditions of use.
-
When planning to upgrade legacy production, it’s crucial to strike a balance between centralized and distributed computing nodes. It’s advisable to put the advanced analytics applications to the cloud, while real-time operations should be performed at the edge.
-
IoT Gateways were created to connect the machinery with the cloud. The optimal solution here would be to include one or several gateways for the group of machines while connecting them directly through the wireless modem.
-
Connectivity issues might be addressed through the implementation of mesh topology that allows for reliable real-time access for equipment in difficult-to-reach areas.
About Ms. Julia Mitchell
Julia is Business Operations Manager at Professional Software Associates Inc. (PSA). She is eager to solve clients’ business challenges by building full-fledged IoT ecosystems. Having 8+ years' experience in the EIoT development industry, Julia is involved in projects in the Automotive, Energy, Logistics, & other domains.
The content & opinions in this article are the author’s and do not necessarily represent the views of ManufacturingTomorrow
Comments (0)
This post does not have any comments. Be the first to leave a comment below.
Featured Product
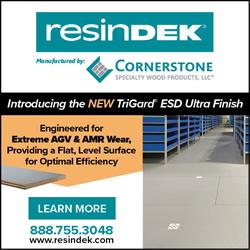