The future of additive manufacturing is all about design
Guidelines for implementation of Industry 4.0
World's Largest Search Engine for 3D Printable Models Launched
What's holding back growth of 3D printing and additive manufacturing?
Smart Factories to add $500 billion to the global economy in next 5 years
IoTium Delivers Industry's First Secure, Scalable, Network Infrastructure for Industrial IoT
NASA Awards $100,000 in 3D-Printing Habitat Competition
To 3D Print or Not to 3D Print?
The Blackbelt lets you 3D print really long items
Robotics, AI and 3D printing could close UK's productivity gap
Elon Musk: Robot software will make Tesla worth as much as Apple
Apple starting US tech manufacturing fund with $1 bn
Why Germany Still Has So Many Middle-Class Manufacturing Jobs
LINK3D Launches Largest Platform To Connect Engineers With Global Additive Manufacturing Services
Fanuc Leads The Way For Smart Factory Software For Now, Kuka And ABB To Follow Closely
Records 916 to 930 of 1242
First | Previous | Next | Last
Featured Product
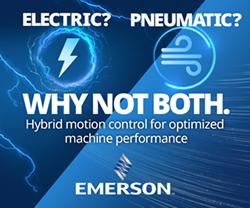