Debunking Concerns About the Use of Abrasive Finishing Tools in CNC Applications
Take Advantage of Current CNC Machining Trends
Tips to Save Money on Your Next CNC Milling Project
Smart Manufacturing Control
New Tools for Tooling Help Boost Manufacturers Bottom Line
Safeguard your digital future now. Overcome the crisis!
How digital connects CNC businesses in the age of the pandemic
Case Study: Phase Four Launches Scalable Electric Propulsion (EP) System with Xometry
Diode Lasers in CNC and 3D Printing
Diode Laser on your 3D Printer, Perfect Tool for Makers?
2018 Used CNC Machine Price: Average CNC Machine Price
Future Forward: CNC Machines
Machine Shops Must Prepare for Industry 4.0
The Slow Growth of High Speed
The Rise of 5
Records 31 to 45 of 61
First | Previous | Next | Last
Featured Product
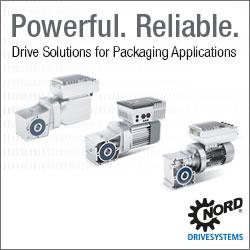