The Top 5 Things Every Manufacturing CIO Should Know
4 tips for developing predictive analytics in manufacturing
How IoT Will Elevate 8 Types of Equipment in 2023
Raising the Roof (on Network Capacity) - New "Indoor Backhaul" System to Help Meet Rapidly-Growing Bandwidth Requirements for IIoT Applications
Robotics In Manufacturing: Threat or Opportunity?
It's All Connected: Care, Collaboration, and the Cloud
Could Energy-Harvesting Technology Power IoT Devices of the Future?
Understanding the Role of Machine Vision in Industry 4.0
Strategies for Optimizing Supply Chain with Automation
5 Ways You Can Improve Your Manufacturing Operations with a Data-First Strategy
Ten tips for modernising your HMI/SCADA system
How Effective Recycling Practices Can Impact the Redistribution of Global Resources and Wealth
MICRO MOLDING - PLACE THE FOCUS ON OUTCOMES
Preparing Your Manufacturing Business for Uncertain Economic Conditions
Patti Engineering and Kettering University Collaborate on Industry 4.0-Enabled Collaborative Robotic Cell for Real-World Learning
Records 286 to 300 of 1242
First | Previous | Next | Last
Featured Product
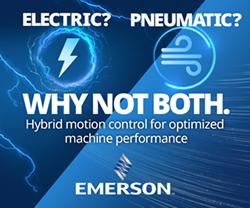