MIT Builds Invisible Fish Grabbing Robot
Why 2017 is the year integration enables Industry 4.0 growth
The 9 unit Winbo 3D printer is an all-in-one micro factory
The Road To IIoT: What Can We Learn From Other Industries?
U.S. investors see more automation, not jobs, under Trump administration
One Of Europe's Top Business Schools Is Helping Executives Navigate Industry 4.0
Adidas reveals plans for 3D printing 'Speedfactory'
Chiefs hold back on smart factories after backlash
Sharp Executive Says Plan for Foxconn LCD Plant in U.S. is Still 'On The Table'
ASU site of largest academic additive manufacturing center in the southwest US
The 3D Printers of CES
3D graphene: MIT scientists develop super-light, super-strong structure
CES 2017 - MarkForged 3D prints metal
3D printer builds a cube from a vat of goo … using a phone screen
Manufacturers most upbeat in two years, ISM survey shows
Records 991 to 1005 of 1242
First | Previous | Next | Last
Featured Product
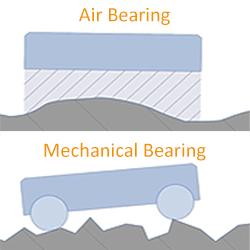