ABB launches OmniCore, a new era of digital robot control to increase flexibility, reliability and performance
ISG to Address Future of 'Digital Factory' at Connected Manufacturing Forum
Simio's 8 Reasons to Adopt Industry 4.0
CRIQ will showcase Canada's first cyber-physical factory at the Montreal Manufacturing Technology Show
ABB to Invest €100 Million in Global Innovation and Training Campus
Sensai Modernizes Manufacturing Operations With AI; Launches US Pilot Program
ManufacturingTomorrow - Special Tradeshow Coverage
MODEX 2018
Smart Factories Need Space and Time Anchors
First Solar Is Using Robots to Better Tap the Sun
Why China's hollowed-out manufacturing hub is pinning its hopes on a hi-tech revival
Analysis: Four smart factory trends to watch in 2018
HP unveils S$100m campus, home to its first advanced manufacturing centre
Huawei Wireless X Labs Sets up Connected Factory SIG to Explore 5G Applications in Smart Manufacturing
What We Can Learn From the Second Life of Google Glass
3D Printer Farms And Robotics Start Pointing To Future Of Manufacturing
Records 61 to 75 of 153
First | Previous | Next | Last
Featured Product
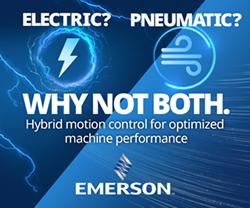