Closing US Manufacturing Trade Deficit Would Create 1.3M Jobs, Says Tech Think Tank
Manufacturers raise investment in next-gen tech, survey says
S. Korea's Hanwha to develop smart factory platform
Number of Smart Factories in South Korea to be Almost Doubled
Five steps to enabling a data-driven, smart factory
Why 2017 is the year integration enables Industry 4.0 growth
The Road To IIoT: What Can We Learn From Other Industries?
U.S. investors see more automation, not jobs, under Trump administration
One Of Europe's Top Business Schools Is Helping Executives Navigate Industry 4.0
Chiefs hold back on smart factories after backlash
Sharp Executive Says Plan for Foxconn LCD Plant in U.S. is Still 'On The Table'
YCF - 2017 could be year of smart factory
What are the business and security impacts of Industry 4.0?
Japan's Rust Belt Counting on Robonomics to Run Assembly Lines
A New Use for High-Speed Fiber Optics: Connecting Smart Factories
Records 556 to 570 of 665
First | Previous | Next | Last
Automation & IIoT - Featured Product
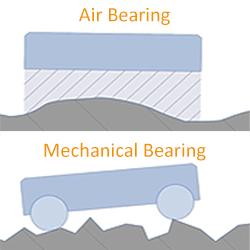