The Smart Move to More Efficient and Safer Maintenance Operations
How to Break Free From the Dependence on Intuition and Unique Skills in Maintenance Work
Tips For A Successful Preventative Maintenance Strategy
How To Improve Production With Autonomous Maintenance
How to Keep Your Manufacturing Plant Clean
Challenges of PLM Integration
Condition Based Maintenance (CBM)
Maintenance in the Digital World
Metal Additive Manufacturing Powder Recovery Equipment
Seven Key Considerations When Choosing the Right Equipment Lubricant
How to Effectively Clean and Maintain Manufacturing Equipment
Using IoT for Machine Learning-based Predictive Maintenance
Hose Failure Can Halt the Manufacturing Process … Don't Let It Happen
Why Startups Are the Future for the Industrial Internet
Predictive Maintenance, the 1st Step Towards Self-Maintenance and AI
Records 16 to 30 of 36
First | Previous | Next | Last
Featured Product
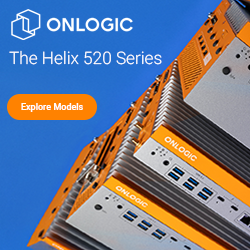