Why does maintenance work tend to become narrowly focused so that it becomes virtually inaccessible to most people?
How to Break Free From the Dependence on Intuition and Unique Skills in Maintenance Work
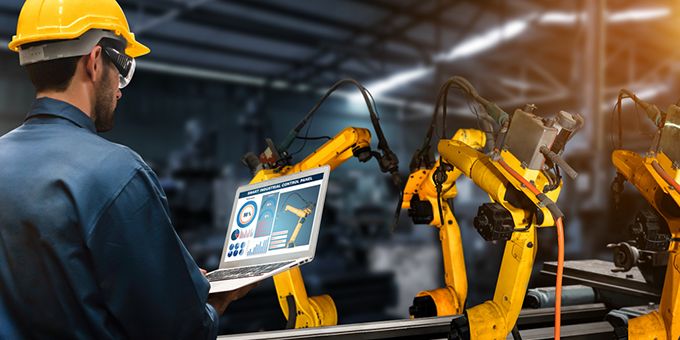
Article from | Murata
Maintenance work involves responding to breakdowns in factory equipment. This field tends to have a shortage of staffing and a reliance on unique skills, and this often leads to a dependence on the intuition, experience, and unique skills of the individual maintenance technician. Even so, when thinking about boosting the competitiveness of factories and improving their productivity in the years ahead, an important keyword has become “standardization” for enabling a wider range of people to be involved in maintenance work, rather than relying on the intuition and unique skills of certain select people. That is how it is explained by Kenichi Furutani, a consultant at Japan Excel-Management Consulting (JEMCO), who is known as an expert in enhancing factory performance. We talked to him about how to break free from the dependence of maintenance work on intuition and unique skills, and how IoT should be used to achieve this.
Why does maintenance work tend to become narrowly focused so that it becomes virtually inaccessible to most people?
--Mr. Furutani has provided consulting services to many companies, primarily in the manufacturing industry. I think that you may be looking at a wide range of issues from upstream management to on-site operations, but is maintenance work such as inspection and repair of equipment often the key to making improvements there?
I feel it is quite significant. However, it is a rare case when a company comes to us from the beginning with a request to improve its maintenance work. Rather, in many cases, maintenance is the result of discussions and pursuit of what the factory should be and what it should do to increase its competitiveness and productivity. It is only when you think deeply about the future and the essence of the factory that you realize the challenges facing maintenance work.
In particular, it is expected that high-mix low-volume production and individual production where required quantities are produced on an as-needed basis will increase in the future. As the manufacturing process becomes more complex, the equipment also becomes more complex and sophisticated. When that happens, the key to competitiveness will be maintaining this equipment and achieving stable operations. If we think about the state of our factories over the long term, looking several years into the future, we need to redefine the position of maintenance for the company as a whole.
In general, the area of maintenance has been the most difficult to address, and it is also an area that is often put off. That’s why it is often left in a poor situation and requires considerable effort when reforms are finally implemented.
Why is maintenance so hard to address and often put off?
The key issue for many factories is to maintain daily production and operations, and so they inevitably prioritize their work for this purpose. Even if we perform the necessary maintenance work every day, the maintenance work performed when a problem occurs is not needed until something goes wrong. In these types of situations, maintenance work is often put off and there are not enough maintenance technicians; as a result, there are many factories where only a limited number of technicians are in charge of the maintenance of the entire factory.
Nevertheless, maintenance technicians are required to have a great deal of knowledge, experience, and expertise. They must know the structure and characteristics of all types of factory equipment and be able to solve problems quickly. However, if only a few people oversee maintenance work, the knowledge and expertise accumulated in the process of the work will not be shared. As a result, the work of maintenance technicians develops into a state of limited accessibility. This is what we call the dependence on intuition and unique skills in maintenance work.
What exactly are the problems caused by the dependence on intuition and unique skills?
For example, large-scale replacement of factory equipment is not done very often; therefore, many factories continue to use machines that are quite old for many years.
In such factories, it is not uncommon for drawings and manuals for equipment to be lost, and in some cases, authorized parts are no longer available for replacement. In these cases, the maintenance technicians add their own parts or make repairs whenever a failure occurs. When this happens, the original specifications of the machine will not be known to anyone other than the maintenance technician, and operation of the machine will depend on the intuition and unique skills of the technician, which will make the limited accessibility even worse. This is extremely problematic.
When production problems such as short stoppages occur frequently due to equipment trouble, we sometimes take measures to return the equipment to its initial state. In these types of situations, if there are no drawings and only a few technicians know the true state of the machine, this will entail a tremendous amount of work. This is especially true if the maintenance technician has already retired or left the work site.
Consequently, the machine becomes a black box that is accessible only to select maintenance technicians.
As I mentioned earlier, few companies provide much available staff or resources for maintenance. In these situations, failure to share maintenance expertise will be detrimental to the operation of the plant. The number of tasks that can be done only by the maintenance technicians increases, and they always have their hands full, only repairing machines after they have broken down. In other words, it’s like trying desperately to bring failures, a negative state, back to zero, and it never turns into a positive in terms of productivity.
To increase the productivity of a factory, the operating rate must be increased. To achieve this, equipment breakdowns must be prevented, and maintenance work should play a role in this process.
So instead of reducing the negative, it is important to prevent breakdowns so that a negative situation does not occur in the first place?
That’s right. Maintenance can be divided into three main types. Reactive maintenance(Corrective maintenance/ Breakdown maintenance) is the process of dealing with problems after they have occurred. Preventive maintenance is used to prevent problems before they occur by periodically performing prescribed maintenance tasks. Predictive maintenance is the process of recognizing problems before they occur and preventing them from happening in the first place. There is nothing better than being able to perform preventive and predictive maintenance rather than reactive maintenance. However, when a state of limited accessibility becomes more prevalent in the maintenance work, it is easy to get caught up in reactive maintenance work, which in turn makes it difficult to boost equipment operation, thus creating a vicious cycle.
IoT as a methodology to break free from dependence on intuition and unique skills
How can we break away from this dependence on intuition and unique skills, share expertise, and standardize maintenance work so that more people can be involved in maintenance?
First, it is necessary to thoroughly identify the work processes of maintenance. In other words, you can say that intuition and unique skills are tacit knowledge that depends largely on the knowledge and experience of the individual. In other words, this is knowledge that is not clearly verbalized, but that only maintenance technicians comprehend.
And so, this tacit knowledge must be converted into formal knowledge that other people can understand. For example, there are many ways to document the maintenance process, such as creating a procedure manual, or keeping a record of every step of the maintenance process with photos and notes. What is important is where tacit knowledge occurs in the process of maintenance work, and where dependence on intuition and unique skills occurs. It’s about figuring this out.
And so, the foundation for everything is verbalizing the maintenance work and knowing what tacit knowledge is?
That’s right. However, this is not an easy task either. Verbalizing maintenance expertise is not a straightforward task. There are many cases where a maintenance technician writes something down thinking that others will understand it, but it is not conveyed to people unfamiliar with maintenance work, or the technician himself or herself is not aware of what tacit knowledge is in the first place.
When I provide consulting services, I strongly advise that when creating procedure manuals and other documents, they should be written in a basic and straightforward way that anyone can understand. It is vital to identify work processes in detail and reliably so that any person can reproduce them by following the written instructions. Intuition and unique skills are not found in poor-quality manuals and procedures, and it is extremely important to provide visualization using words and illustrations.
This is a process that requires a lot of perseverance to implement.
One thing that I am focusing on in breaking from the dependence on intuition and unique skills is the use of IoT technology. I believe that IoT has the potential to not only eliminate the limited accessibility of maintenance, but also to dramatically raise the level of maintenance work by enabling predictive maintenance.
For example, let’s say you have a sensor attached to a machine to acquire vibration data. It then compares the data with that of past failures and sounds an alarm when the vibration is close to that of the failure. Of course, in reality, data analysis is not quite so simple, but this is a simple example of IoT, which is exactly what predictive maintenance should be.
However, preventive maintenance is also effective in preventing breakdowns, but in some cases it may make the work of maintenance technicians busier because they must check and inspect the machine periodically regardless of its condition. In situations where there are few people to devote to maintenance, we must consider the negative effects that sometimes occur.
Then, predictive maintenance is the most efficient way to predict and prevent failures, and IoT is the best way to support this?
IoT uses data to visualize what used to depend on the intuition and unique skills of maintenance technicians. It will also lead to the improvement of the quality of maintenance work. Of course, it is as important as ever to develop human resources, such as by training high-level maintenance technicians, but it is obvious that Japan will become increasingly short of human resources in the future due to the declining birthrate and aging population, and it will take time to train them. I think it would be ideal if we could use IoT as a complementary solution and train human resources at the same time.
The dependence on intuition and unique skills leads to limited accessibility of maintenance work. I realized that for factories to be competitive in the future, it is important to change the tacit knowledge of intuition and unique skills into formal knowledge to achieve a higher level of maintenance. And the key to this is the use of IoT.
The content & opinions in this article are the author’s and do not necessarily represent the views of ManufacturingTomorrow
Comments (0)
This post does not have any comments. Be the first to leave a comment below.
Featured Product
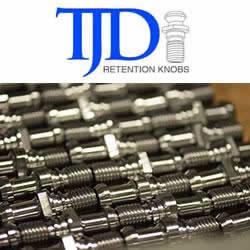