Tips For A Successful Preventative Maintenance Strategy
A successful preventative maintenance strategy involves much more than a couple of mechanics lubing your machinery moving parts on the production line. Preventative maintenance is a comprehensive and facility wide program that ensures that you’re protecting your investment dollars and supporting the bottom line of your facility, including ensuring the health and well-being of all associates working on the production line.
When you’re implementing a new preventative maintenance strategy, the task can often seem daunting, even overwhelming at some points in the project. However, these 10 tips should help give you a push in the right direction and help you cut through to the heart of the PM strategy tasks.
Break Entire Facility Into Areas
Assign each room or area of the facility a location tag. For example, your main lab can be ML-01. This enables you to assign each asset to a particular area, which will tell every mechanic with a preventative maintenance work order exactly which area they can report to and locate the particular asset on the work order. It also ensures correct departmental charging for parts and labor, as we link each area to a particular cost center. In this case, the main lab would own the asset being maintained, therefore, the charge would be absorbed by the cost center for the main lab.
Make an Inventory Of Everything
Inventory every piece of equipment, not just the moving machinery, but items such as vats, tanks, and CIP lines so that every single item has its own asset number and asset tag. This is a time-consuming task, and can be greatly assisted with a current asset drawing being used for the larger pieces of equipment, and all stationary equipment in the facility.
Make Your Manuals Digital
All equipment manuals need to be transferred to electronic form, or requested in electronic form from the equipment manufacturer. Many equipment manuals include diagrams, such as parts diagrams for rebuilds and ordering replacement preventative maintenance parts. These are absolutely vital to the success of your preventative maintenance program, and will also greatly reduce the task load on your parts department.
Communicate With Manufacturer
Once you have all manuals on hand in electronic form, request any missing manuals or documentation from the manufacturer. All of the equipment inside of your facility should have a manual associated with it. If you don’t have one, request one.
Use CMMS
System Administrators do much more than simply key data about the facility into a CMMS. A system administrator is vital in a successful preventative maintenance strategy. As your facility is constantly changing and updating, a system administrator has the task of ensuring that the information in your CMMS database is changing and updating along with it. They play a key role in your maintenance program success, and without them, it is very easy to end up with outdated or irrelevant information in your CMMS.
Keep Up With Technician Training
All of the software in the world can’t make up for technicians who don’t know how to repair a new piece of equipment because they weren’t sent to the training class. You ensure the success of your maintenance program by keeping skilled technicians on your team.
Get Rid of Outdated Equipment and Maintenance Files
They’re not serving any purpose when a work order for a machine you sold 5 years ago pops up, requesting service for equipment long since removed. There is a place for outdated files, and that is the old filing cabinet in the dark corner of the basement.
Review, and Set New KPI’s.
It’s imperative to keep your eye on your key performance indicators, and to set new goals for your preventative maintenance strategy as you achieve your current goals. By ensuring that there are goals to be met, you’re also ensuring that your team is being held accountable for the health of your machinery.
Review, then modify.
Not every maintenance task is a helpful maintenance task. It is important to regularly review what is working and what isn’t, and to make changes accordingly. Don’t be afraid to recognize outdated or inefficient processes, and to focus on the betterment of your facility as a whole. As your facility grows and changes, your preventative maintenance strategy should do the same.
Verify the Current Preventative Maintenance Strategy Timeline
Not every piece of equipment on your production line is going to be found to be within the manufacturer's guidelines. That’s simply a part of maintenance. People take vacation, important tasks get pushed aside for more important tasks. Be certain to regularly review the maintenance schedule and verify that the tasks that are being performed are adhering to the schedule that the manufacturer suggests. If the PM schedule isn’t following the manufacturer's suggested timeline, make it a point to change that.
--
Talmage Wagstaff.
Co-Founder and CEO of REDLIST. Raised in a construction environment, Talmage has been involved in heavy equipment since he was a toddler. He has degrees and extensive experience in civil, mechanical and industrial engineering. Talmage worked for several years as a field engineer with ExxonMobil servicing many of the largest industrial production facilities in the Country.
Comments (0)
This post does not have any comments. Be the first to leave a comment below.
Featured Product
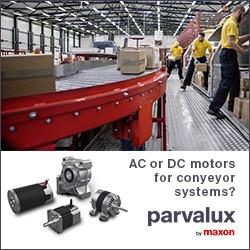