AM Research Publishes In-Depth Market Study on Additive Manufacturing for Military and Defense; Estimates $0.3B in Direct DoD Spend in 2023, Growing to $1.8B in 2032
The comprehensive study sheds light on the rapid evolution and potential impact of additive manufacturing technologies on the defense and military landscape.
How Additive Manufacturing Can Step Up to Print Emergency Replacement Parts in the U.S. Military
Technological innovation in the U.S. military is revolutionizing defense, responding to natural disasters, and so much more, but it also creates unique challenges. 3D scanning combined with additive manufacturing (AM) can step in to print emergency replacement parts.
Evolution of the Need for Expeditionary Manufacturing
There is a demand signal to produce a machine capable of Metal printing on the front lines. Phillips has developed a Hybrid technology that adds a Wire fed Direct Energy Deposition head to a Haas machine.
ExOne Developing Portable 3D Printing Factory in Shipping Container for Department of Defense
ExOne has been awarded a U.S. Department of Defense contract to develop a fully operational, self-contained 3D printing "factory" housed in a shipping container. Now under development.
U.S. Army Research Lab Selects 3D Systems to Develop World's Largest, Fastest Metal Powder 3D Printer
United States government invests $15 million towards the development of the next generation of metal 3D printing technology - advancing U.S. competitiveness and national security.
How to Keep Your Manufacturing Site Secure in the Age of the IIoT
Manufacturing sites of all kinds now find themselves potentially vulnerable to new types of cyber-attacks - the kinds that turn our own connected devices and equipment against us.
GE Awarded $9 Million from Office of Naval Research to develop framework enabling the rapid qualification and certification of 3D Printed Parts
3D printing could replace legacy manufacturing processes no longer in use to produce decades-old replacement parts
The US Navy 3D printed a concept submersible in four weeks
Andrew Liptak for The Verge: The team began work in August 2016, and used a massive industrial 3D Pinter called Big Area Additive Manufacturing (BAAM) to manufacture six carbon fiber sections, which were then assembled into the 30 foot long vehicle.
Researchers fire 3-D printed ammo out of a 3-D printed grenade launcher
Mr. Seung kook “Sunny” Burns and Mr. James Zunino for US Army Blog: Researchers at the U.S. Army Armament Research, Development and Engineering Center (ARDEC) successfully fired the first grenade created with a 3-D printer from a grenade launcher that was produced the same way. This demonstration shows that additive manufacturing (commonly known as 3-D printing) has a potential future in weapon prototype development, which could allow engineers to provide munitions to Soldiers more quickly.
The printed grenade launcher, named RAMBO (Rapid Additively Manufactured Ballistics Ordnance), was the culmination of six months of collaborative effort by the U.S. Army Research, Development and Engineering Command (RDECOM), the U.S. Army Manufacturing Technology (ManTech) Program and America Makes, the national accelerator for additive manufacturing and 3-D printing.
RAMBO is a tangible testament to the utility and maturation of additive manufacturing. Cont'd...
Records 1 to 9 of 9
Featured Product
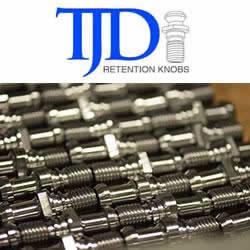
T.J. Davies' Retention Knobs
Our retention knobs are manufactured above international standards or to machine builder specifications. Retention knobs are manufactured utilizing AMS-6274/AISI-8620 alloy steel drawn in the United States. Threads are single-pointed on our lathes while manufacturing all other retention knob features to ensure high concentricity. Our process ensures that our threads are balanced (lead in/lead out at 180 degrees.) Each retention knob is carburized (hardened) to 58-62HRC, and case depth is .020-.030. Core hardness 40HRC. Each retention knob is coated utilizing a hot black oxide coating to military specifications. Our retention knobs are 100% covered in black oxide to prevent rust. All retention knob surfaces (not just mating surfaces) have a precision finish of 32 RMA micro or better: ISO grade 6N. Each retention knob is magnetic particle tested and tested at 2.5 times the pulling force of the drawbar. Certifications are maintained for each step in the manufacturing process for traceability.