Complete Guide to Gas Mixing and Blending
Improving Manufacturing Productivity
Automation in Forging Industry Speeds Production and Increases Safety
Big Picture Benefits of a CMMS
Thermoplastic Extrusion 3D Printing
IoT & Industry 4.0
Bringing Manufacturing Back Home
Why Data Empowerment Matters
A Disruptive AM Technology for Micro Manufacturing
Tips and Tricks for Selecting a Process Manufacturing ERP
What will SCADA of the future be like? (Third Part)
Automate 2019 with Emulate 3D
Automate 2019 with Bosch Rexroth
Automate 2019 with KingStar
Complex Metal Parts with Internal Passageways, Built Layer by Layer
Records 181 to 195 of 554
First | Previous | Next | Last
Featured Product
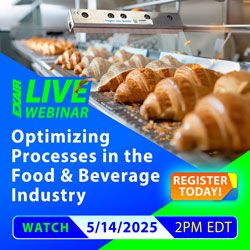