Safety solutions for intelligent human-robot collaboration
Hirose, Harting Team Up on 10 Gbit Ethernet Connector Standard
Factory Equipment Maintenance and Industry 4.0
New technologies reshape production lines
How to prepare a business for an Industry 4.0 network
Data, Digital Threads and Industry 4.0
Industry 4.0 - Interview with fabb.one Ltd
Do the benefits of robotics outweigh the heavy demands on infrastructure?
IISc building India's 1st smart factory in Bengaluru
Industrial digitisation on fast track
Where do you get the I/O for the IIoT?
Schneider Electric's three steps for implementing Industry 4.0
10 Ways Machine Learning Is Revolutionizing Manufacturing
Companies, employees not quite ready for cognitive technology wave of robotics, AI, machine learning
'UK manufacturers fail to understand Industry 4.0'
Records 136 to 150 of 201
First | Previous | Next | Last
Featured Product
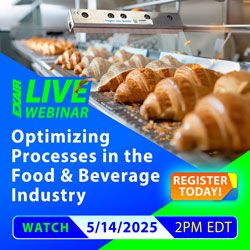