Innovation in Creation: Demand Rises While Prices Drop for 3D Printing Machines
Buildings Manufactured From A 3D Printer
3D printing software, sensors, and carbon nanotubes among top Advanced Materials trends of 2016
Is Velo3D Plotting a 3-D Printed Robot Revolution?
Volvo Construction Equipment Digs Up Prototype Savings Of 18 Weeks And 92% Of Costs
Thoughts turn to revolution in Davos
New Ultrasonic 3D Printing Process Can Create and Print High-Tech Composite Materials
For Advanced Manufacturing, Success Demands Innovation, Education and Public-Private Partnership
Special Tradeshow Coverage for Advanced Manufacturing Conference & Expo 2016
3D Printing of Motors and Electronics
Robotic Additive Manufacturing Platform for 3D Printing Composite Parts
3D Printing and Acoustics: Rapid Prototyping of Sound Diffusers
Rob Scharff's Soft Robotics 3D-printed hand responds to human grip
Cisco Teams Up with Robotics Firm Fanuc for IoT
RoboSAM Can Assess Its Situation and Call a Human for Help When It Needs Assistance
Records 631 to 645 of 779
First | Previous | Next | Last
Additive & 3D Printing - Featured Product
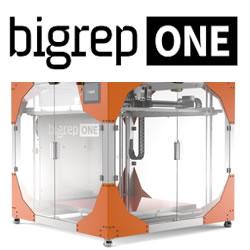