OMRON to Introduce 15,583 Models in 7 Categories to World, Second Wave of FA Devices Built on Common Design Platform
New modular AM 'smart factory' from Concept Laser decouples pre-production and production
Peugeot Teams Up With 3D Printing Startup for Parts and Possibly Full Cars
Safety solutions for intelligent human-robot collaboration
IIoT and Industry 4.0 to Create Growth in Telerobotics in Manufacturing
Oak Ridge tool takes world record for largest 3D-printed object
Why manufacturing will make or break the future of energy
Going Beyond 3D Printing to Add a New Dimension for Additive Manufacturing
New technologies reshape production lines
How to prepare a business for an Industry 4.0 network
This Time, 3D Printer Makers Think They Found a Sweet Spot
IISc building India's 1st smart factory in Bengaluru
OpenKnit: Open Source Digital Knitting
Have we solved the nanomaterials problem?
Norsk setting up industrial scale additive manufacturing plant in New York
Records 331 to 345 of 384
First | Previous | Next | Last
Supply Chain - Featured Product
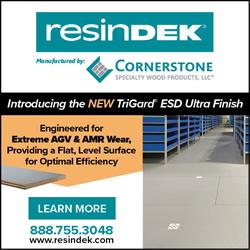