New High Accuracy Hexapod for Optics and Photonics Alignment is Compact
Engineered by PI for test and assembly of high-resolution optics and photonics components.
PI has introduced an ultra-high-resolution, high-stability hexapod to complement its family of compact hexapods. Designed specifically for the precise alignment of high-resolution miniature lenses and photonics components, the H-811.S2iHP hexapod utilizes six low-friction, long-life actuators, and 12 precision cardanic joints with offset axes, ensuring enhanced stiffness.
Superior Resolution and In-Position Stability
This hexapod is engineered to achieve superior precision and stability. Its actuators provide a resolution of 1.4 nanometers, and the platform delivers in-position stability of 3 nanometers.
With a maximum velocity of 20 mm/sec, fast acceleration, and a load capacity of 5.5 lbs., the H-811.S2iHP is ideal for tasks like alignment, testing, and assembly of miniature optics and photonics components. Despite its compact size, it offers linear travel ranges up to 34mm in XYZ and rotary motions (pitch, yaw, and roll) up to 42°. A user-programmable pivot point further facilitates alignment of lenses, fiber optics, and photonics systems.
High Duty Cycle Design for Industrial Alignment
Designed for industrial precision alignment applications, the hexapod incorporates low-friction precision ballscrews, precision joints, and long-life brushless motors to ensure reliability and durability.
Advanced Controller for Alignment Optimization
The H-811.S2iHP is paired with a powerful hexapod controller featuring advanced multi-axis alignment routines at the firmware level. These routines enable tasks like first light detection, optimization, tracking, and array alignment, making the hexapod an ideal tool for automated photonic and optical alignment tasks.
How Hexapod Parallel Motion Systems Work
Hexapods are 6-degree-of-freedom (6 DOF) motion systems capable of movement in XYZ and rotations in pitch, yaw, and roll. They are based on actuators arranged in parallel between the top and bottom platforms and controlled by a powerful controller handling the hexapod kinematics - so the user only needs to send commands in common Cartesian coordinates.
Available in various sizes, from base diameters of 100 mm to 1 meter, and load capacities up to 2 tons, PI hexapods are versatile solutions for complex multi-axis precision motion needs. Equipped with state-of-the-art controllers and software tools based on 30+ years of R&D, these systems enable fast and precise implementation across diverse applications, from medical devices to photonics.
PI Hexapod Key Features
Cartesian coordinate control for all six axes
Dynamic, software-configurable center of rotation
Easy connectivity -- only 2 cables for all 6 axes
Elimination of friction and torque caused by cable drag
Higher stiffness and dynamics than comparable serial kinematic positioning systems
Central aperture
PI hexapods continue to set the standard for innovation in multi-axis precision motion systems.
Industries Served
Photonics, Optics, Silicon Photonics, Microscopy
PI Americas
https://www.pi-usa.us | info@pi-usa.us | (508) 832-3456
Featured Product
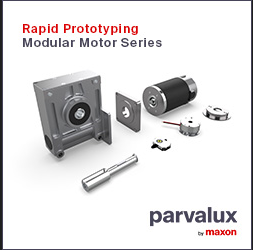
Rapid Prototyping with the Modular Motor Series
Quick to configure. Quick to build. Quick to deliver. Parvalux understands the importance of getting product in the hands of customers quickly and efficiently. The Modular Range does just that allowing customers to configure their own solution, selecting motor and gearbox, adding encoders and brakes to create a solution perfectly suited for their specific applications such as conveyor belt systems, picking systems, parcel sorting equipment, pallet shuttles and automated storage and retrieval systems (ASRS). Read our modular range guide for specifics.