Acty launches Work Instructions, the new function to simplify production operations
Acty's Work Instructions enable manufacturing companies to digitize the maintenance process and offer technicians simple maintenance procedures that are available H24.
Acty (www.acty.com), a leading provider of augmented reality digital solutions for manufacturing and industrial operations, is pleased to announce the launch of its new Digital Work Instructions feature. Designed to simplify and streamline complex procedures, Acty's Work Instructions provide clear step-by-step guidance to ensure consistency and quality across all activities.
Work Instructions are an electronic evolution of workflows, procedures, and manuals useful for technicians in the field to immediately receive all the information they need to perform complex tasks in real-time.
A step toward the digital future of Service in Industry 4.0, able to innovate service processes, improve complex procedures, and bring attention to the environment by significantly limiting travel and transfers to get efficiency and focus on improving services and, therefore, the business generated.
WHAT IS ACTY?
Acty was born out of the industrial sector's need to speed up maintenance, repair, and installation procedures, which, according to the current model, most often require the intervention at the company of an expert.
Typical situations are those that require manual intervention of mechanical, electrical, hydraulic parts for problems that one is not able to solve independently, without the call of an expert.
This, for the service of companies, results in travel, dedicated expert time, additional costs and a consequent loss of efficiency, without being able to offer customers a H24 service with which to solve problems even in the off-hours situation.
"Alway Close To You" is how the company's slogan reads and is also the acronym behind the name of this cloud service. And this is also its main goal: to be always close to companies in their need for remote support, to enable its technicians to solve even particularly complex problems without the need for losses.
THE NEW WORK INSTRUCTIONS FEATURE
Having detailed work instructions is an essential part of any manufacturing process, as they explain the best way to complete a specific procedure in a standardized way, helping technicians perform complex tasks.
Acty's Work Instructions are designed to address these needs and provide the ability for technicians and customers to perform tasks on their own, reducing repairs and maintenance and relieving the experts in the companies that supply machinery to give support for recurring class problems that are not complicated to solve.
Each company can design its Work Instructions by combining different visual elements, images, videos, pdfs, data entry, media captures, and checklists to provide the most information to technicians and enable them to perform even the most complex procedures.
Making and publishing Work Instructions in Acty is very quick and fast because it starts with an intuitive editor that allows you to use preset templates as a starting point for creating digital work instructions for:
- Manuals
- Maintenance Operations
- Troubleshooting
- Audit Checklists
- Safety Checklists.
Despite the simplicity of Acty, the task of creating Work Instructions is a time-consuming and concentration-intensive activity. Icona offers its support with its own team in charge in order to outsource the creation of Work Instructions for companies.
ACTY, READY TO RESPOND TO ANY NEED
The idea behind Acty is thus a remote support service for any kind of need from the technical point of view of maintaining one's industrial equipment.
What it makes available are functions that can be used with the simple use of one's smartphone or computer, by downloading the dedicated app or using the software directly from the web. Chief among these is definitely AR remote support, which allows an expert to provide instructions and assistance remotely, thanks to the online platform that puts him or her in direct communication with the operator.
In addition, thanks to the possibility of integrating Acty's functionality with the use of smart glasses, the technician will have the enormous advantage of being able to have his hands free while showing on video what is in front of him. In this way, the expert will be able to offer his assistance in real time, directly observing the issue and being able to give precise and detailed instructions.
Not only support, Acty also offers an instant translation service for messaging in more than 60 languages, the ability to communicate simultaneously with multiple experts, pausing calls, and track and record one's movements so that one is fully assured of not making any mistakes.
"Acty has enabled us to enter the heart of manufacturing industries' support services by bringing innovation and efficiency," said Icona CEO Giorgio Nepa. "Our challenge is the continuous search for new and concrete innovations, make them available to our customers in order to accompany them in the process of digital transformation, improve processes and business in after-sales services."
Never alone again, Acty is always near you.
Featured Product
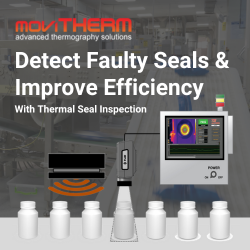
Thermal Seal Inspection for Improved Quality and Efficiency
MoviTHERM's Thermal Seal Inspection (TSI) solution provides precise and reliable detection of defects in a variety of packaging types, including pouches, bags, blister packs, bottle caps, and more. By detecting defects in your packages, the TSI solution helps increase efficiency in your production line and ensures top-quality packaging is delivered to your customers every time. With state-of-the-art technology and an experienced team, MoviTHERM is dedicated to delivering accurate inspection solutions and peace of mind to its clients. Contact MoviTHERM today to learn more about their thermal seal inspection solution.