Robotic Screwdriver Capable of M0.6-M1.6 with Built-In 100% Quality Feedback
Programmable Smart Screwdriver does work and verifies the quality of that work at the same time.
SMAC Moving Coil Actuators has launched sales of Z-theta linear rotary actuators capable of automated assembly of small screws, size range M0.6-M1.6, with real-time feedback on the process to ensure 100% quality feedback. The "robotic screwdriver" could be used to automate micro-screw drilling, tapping, thread check, and screw tightening. SMAC predicts that the smart screwdriver is a breakthrough for assembling precise products such as medical/implantable devices and wearable devices that require sub millimeter screw (M0.6).
Small screw driving is mostly a manual operation today. Major quality problems are cross threading and/or too much torque (which breaks the screw). These problems are overcome by the SMAC solution. The SMAC solution is especially useful for M1.6 or smaller micro screw assembly as this size is outside human worker assembly limits. SMAC smart screwdriver could provide more than expert worker level quality.
The patented technical benefits of the screwdriver to companies both making and using small hole screw driving systems include: the ability to move a small screw - as small as M0.6 - to the tapped hole and perform a Soft-Land routine, the ability to engage screw-threads and hole-threads to prevent cross threading, the ability to thread match, the ability to screw into threads with programmed torque, the ability to check number of turns and depth, the ability to "snug" screw when required, the ability to set programmed final torque and verify movement after this torque is applied, and the ability to report by on the success of the above in real-time.
SMACs built-in sensor feedback system, standard on all their actuators, gives SMACs Moving Coil Actuators the unique mechatronic ability to "do work and verify its success at the same time." This would allow the actuators to quality check key processes 100% in real-time and feedback the results.
Featured Product
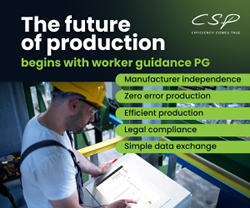