With IO-Link Wireless, food manufacturers and distributors can optimize their processes and stay ahead of the competition. The CoreTigo team provides a comprehensive look at how this works in a real factory setting.
Benefits and Applications of IO-Link Wireless in the Food Industry
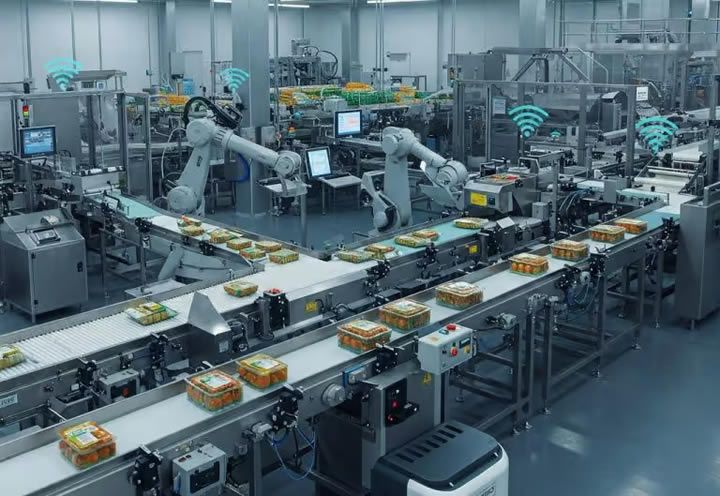
Gabi Daniely, Chief Strategy & Marketing Officer | CoreTigo
IO-Link Wireless technology has been transforming manufacturing environments for many years. The food industry is one of the niches that benefited from this wireless tech the most. Since the industry players are constantly under pressure to reduce costs and improve efficiency while meeting stringent hygiene standards, they always appreciate a high-tech solution. With IO-Link Wireless, food manufacturers and distributors can optimize their processes and stay ahead of the competition. The CoreTigo team provides a comprehensive look at how this works in a real factory setting.
What is IO-Link Wireless?
IO-Link Wireless is an extension of the IO-Link communication protocol designed to connect sensors and actuators to industrial control systems wirelessly. It offers deterministic communication with low latency, supporting flexible production environments.
Benefits of IO-Link Wireless in the Food Industry
As the food industry embraces digital transformation and seeks smarter manufacturing setups, IO-Link Wireless offers tangible advantages. The most important benefits are:
Maintenance Reduction
In food production environments, frequent cleaning cycles are essential to hygiene maintenance. Traditional wired systems require operators to clean cables, routing boxes, and conduits regularly. This adds to maintenance workloads. IO-Link Wireless reduces the number of cables on the production floor. This directly translates into fewer cleaning tasks and less wear and tear on physical components. As a result, food industry players enjoy lower maintenance costs and less downtime. Meanwhile, the staff can focus more on production rather than upkeep.
Cost Savings
Eliminating cables and stainless steel conduits cuts both material and labor costs. Cables and conduits, especially in sanitized zones, are expensive to install and maintain. Deploying IO-Link Wireless reduces the need for specialized materials. It also minimizes installation labor, such as electricians and control engineers. The reduced need for cleaning chemicals and materials further contributes to a reduction in operational expenses.
Complexity Reduction
Retrofitting new sensors or relocating machines in traditional wired setups can be labor-intensive. With IO-Link Wireless, installations are quicker and simpler. Adding sensors or reconfiguring production lines doesn’t require running new cables. Accordingly, the simpler process reduces downtime. This flexibility enables manufacturers to respond to changes in production demands quickly.
Cleaner Production Environment
Food processing facilities have strict sanitation requirements. Fewer cables mean fewer surfaces for dust, food particles, and bacteria to accumulate. By minimizing physical wiring, IO-Link Wireless naturally creates a cleaner workspace. The manufacturers can use this option to enhance food safety and regulatory compliance. This also reduces the risk of contamination.
Seamless Integration
IO-Link Wireless is designed to integrate smoothly with existing industrial systems such as PLCs (Programmable Logic Controllers) and MES (Manufacturing Execution Systems). The interfaces offered by IO-Link Wireless products allow the data to flow easily to management software for real-time monitoring and analytics. This ensures that wireless solutions work in harmony with the facility’s current infrastructure.
Scalable for Future Expansion
As food manufacturers move towards smarter factories, the ability to scale and add new technologies easily is becoming more and more important. IO-Link Wireless supports modular expansions. It allows additional sensors and devices to be integrated quickly. This creates a solid foundation for future applications, such as advanced process monitoring, smart predictive maintenance, and data-driven decision-making.
Applications of IO-Link Wireless in the Food Industry
As food manufacturers aim to boost efficiency and enhance quality control, IO-Link Wireless opens doors to a range of high-impact applications. All of these can bring immediate results AND future-proof production lines.
Wireless Condition Monitoring
In food production, where machinery operates under demanding conditions and unplanned downtime is costly, wireless condition monitoring is invaluable. With IO-Link Wireless, sensors can be installed directly on machines to monitor such parameters as:
- Vibration
- Temperature
- Pressure
- Air Flow
This data is transmitted in real-time to maintenance teams. It helps create predictive maintenance strategies that reduce unexpected equipment failures. Without the need for complex wiring, sensors can be easily deployed even in hard-to-reach areas. This helps maintain consistent production flow and reduces the risk of downtime, which is especially critical in facilities that process perishable goods.
Machine Retrofit and Modernization
Upgrading legacy machinery to meet modern production standards often requires adding new sensors and automation components. In the food industry, where plants may operate for decades, retrofitting is a cost-effective alternative to replacing entire machines. IO-Link Wireless simplifies retrofitting by eliminating the need to run new cables through complex machine architectures. Sensors can be added easily to monitor variables such as flow rates, tank levels, or conveyor speeds. This modernization allows companies to extend the life of existing equipment while improving operational visibility. It also supports incremental upgrades, enabling plants to modernize step-by-step rather than requiring full overhauls.
Mobile and Flexible Production Lines
Many food manufacturers are shifting towards flexible production environments where machinery needs to be relocated or reconfigured frequently to accommodate different products. In traditional wired systems, moving machines can involve cutting cables and rerouting conduits. IO-Link Wireless enables plug-and-play mobility. Machines equipped with wireless-enabled sensors can be moved easily without the need to reinstall cabling. This flexibility supports modular production setups and product-specific reconfigurations. As a result, manufacturers can respond quickly to changing market demands or customer orders.
Quality Assurance and Traceability
Food safety and traceability are critical in the industry to comply with regulatory standards. IO-Link Wireless facilitates real-time data collection from sensors monitoring variables such as temperature, humidity, pressure, and production counts. This data supports better quality assurance processes. It ensures that products meet strict safety and quality standards. Wireless connectivity also enhances traceability, making it easier to track production batches. It helps generate detailed records that support audits and regulatory reporting.
Case Studies
Real-world examples highlight how CoreTigo and IO-Link Wireless deliver value to food manufacturers around the world.
Rotzinger
Rotzinger, a leader in packaging machinery, partnered with CoreTigo to develop an adaptive secondary food packaging machine powered by a linear transport track system. CoreTigo’s IO-Link Wireless technology significantly reduced the need for gears, belts, and external robotic pick-and-place equipment. This streamlined design created a more hygienic machine with fewer hard-to-reach areas requiring frequent cleaning. This is a critical advantage in food production environments. Additionally, the system enhanced flexibility and sustainability. It supported high-speed handling of multiple product variations on a single platform, requiring a smaller footprint per machine and fewer machines, thus reducing the size of the area and equipment requiring sterilization – View Rotzinger Machine in Action
Ulmer Schokoladen
Ulmer Schokoladen, a well-known chocolate manufacturer, leveraged CoreTigo’s IO-Link Wireless technology to retrofit its existing production machines. Their production lines, which require frequent machine relocations, benefited from a wireless setup that eliminated the need for extensive cabling during moves. With IO-Link Wireless, sensors are seamlessly integrated and relocated without complex rewiring. This enables flexible production configurations with minimal downtime and a reduced amount of cabling requiring sterilization. The retrofit approach modernizes legacy equipment quickly and cost-effectively, improving production efficiency while supporting agile responses to changing production needs. Watch the webinar to learn more – View Webinar
The content & opinions in this article are the author’s and do not necessarily represent the views of ManufacturingTomorrow
Comments (0)
This post does not have any comments. Be the first to leave a comment below.
Featured Product
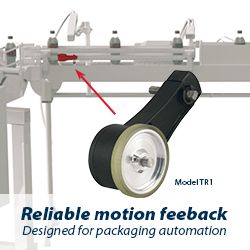