SECS/GEM Software Solutions for Efficient 300mm Tools and Equipment
In the semiconductor industry, the efficient management and control of tools and equipment are vital for optimizing productivity and reducing downtime. One technology that has gained significant popularity is the Semiconductor Equipment Communication Standard (Secs) and the Generic Equipment Model (GEM). This blog post explores how Secs/GEM software solutions can enhance the performance of 300mm tools and equipment, leading to improved operational efficiency and increased production output.
1. Understanding Secs/GEM in the Semiconductor Industry:
Definition and purpose of Secs and GEM
How Secs/GEM standards enable communication between tools and equipment
Key benefits of implementing Secs/GEM software solutions
2. Advantages of Secs/GEM Software for 300mm Tools and Equipment:
Streamlined communication and data exchange: Secs/GEM software enables real-time data collection and sharing between tools and equipment, minimizing delays and errors.
Equipment monitoring and control: The software allows for remote monitoring and control of 300mm tools, enabling proactive maintenance, troubleshooting, and performance optimization.
Enhanced data analytics: Secs/GEM software provides access to valuable equipment data, facilitating advanced analytics for predictive maintenance and process improvement.
Increased productivity and uptime: With efficient communication and real-time monitoring, Secs/GEM software minimizes equipment downtime, leading to higher productivity and improved overall equipment effectiveness (OEE).
3. Integration with Manufacturing Execution Systems (MES):
The role of MES in semiconductor manufacturing
Integration benefits of Secs/GEM software with MES
Combined capabilities for data analysis, scheduling, and optimization
Challenges and Considerations for Implementing Secs/GEM Software:
Compatibility and standardization challenges
Training and skill requirements for operators and maintenance staff
Security Considerations and data protection measures
Case Study: Success Stories with Secs/GEM Software:
Highlight real-world examples of companies that have implemented Secs/GEM software for 300mm tools and equipment and achieved significant improvements in efficiency, productivity, and cost savings.
Future Trends and Innovations:
Evolution of Secs/GEM standards and software solutions
Industry 4.0 and the Impact on 300mm Tools and equipment management
Potential advancements in artificial intelligence and machine learning for predictive maintenance and optimization
Conclusion:
Secs/GEM software solutions have become instrumental in optimizing the performance of 300mm tools and equipment in the semiconductor industry. By enabling seamless communication, real-time monitoring, and advanced data analytics, these software solutions enhance productivity, reduce downtime, and contribute to overall operational efficiency. As the industry continues to evolve, embracing Secs/GEM software will be a crucial step for manufacturers seeking to stay competitive and achieve sustainable growth.
Featured Product
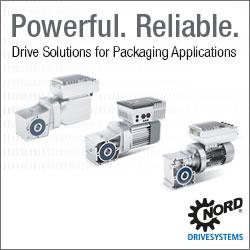
NORD Delivers Powerful, Reliable Drive Solutions for Demanding Packaging Applications
When you need quality, flexibility and high efficiency, NORD has you covered with complete drive solutions for primary and secondary packaging, end-of-line packaging, and higher-level applications. NORD supports you through the entire life cycle of your drive systems with pre-sales engineering support, online tools, and a global service network. Drive systems for both vertically and horizontally networked technology with all the options for sensor incorporation and integration into the higher-level control system.