Implementing corrective actions that are truly sustainable is a constant challenge. There always seem to be variables you didn’t anticipate: A new person executing a process. An important piece of information unexpectedly unavailable. A gap in reporting.
How to Ensure Your Corrective Actions Work, and Keep Working
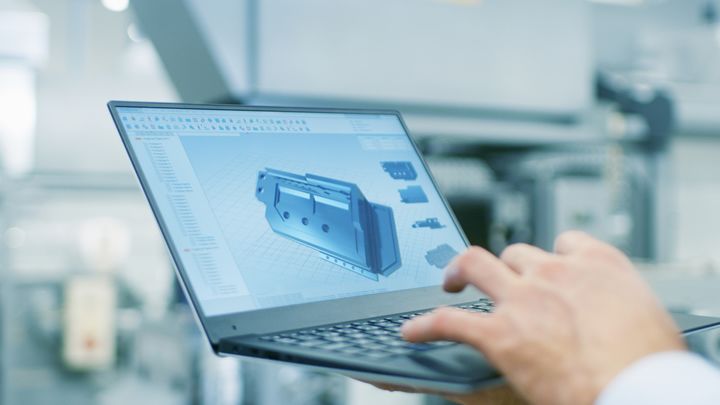
Josh Santo, Director of Industry Strategy & Solutions | Ease.io
It happens often in manufacturing: that quality issue you thought was resolved last quarter resurfaces, this time affecting a customer order. You resolve it asap, but the cycle repeats: issue identification, quick fix, temporary improvement, then back to square one.
Implementing corrective actions that are truly sustainable is a constant challenge. There always seem to be variables you didn’t anticipate: A new person executing a process. An important piece of information unexpectedly unavailable. A gap in reporting.
Where Corrective Actions Fit in Quality Management
We all know that product defects can have huge safety, reputational, and financial consequences. In quality management, the goal is to detect and fix issues and inconsistencies as early as possible in the development and manufacturing process (ideally before they even get to the end product).
When a non-conformance is identified, a root cause analysis (RCA) and corrective actions come into play. RCA and corrective actions serve three critical functions:
- Identifying and eliminating defects
- Preventing workplace safety incidents
- Reducing operational waste through targeted problem-solving
ISO 9001:2015 clause 10.2 mandates this approach, requiring manufacturers to not only correct non-conformities but also eliminate root causes and verify the effectiveness of their actions.
Why Most Corrective Actions Fail
In many operations, quality improvements are managed through spreadsheets, shared drives, and email threads. While this approach might seem adequate, it creates challenges that prevent lasting solutions.
When corrective actions exist in separate systems, contextual information gets lost. Team members search for documentation across departments. Follow-up tasks fall through the cracks. Soon, the same issues resurface, putting the company at risk — again.
This inefficiency costs money. The "1-10-100 rule" of quality costs shows that prevention costs $1, correction costs $10, and failure costs $100. When issues recur, these costs compound.
Creating Corrective Actions That Actually Work
These challenges and risks highlight the need for a more structured, systematic approach to corrective actions, instead of cobbling together various tools and hoping for the best. Here are three ways:
1. Connect the Dots Through Centralized Investigation
Effective corrective actions begin with understanding. When investigating an issue, teams need access to:
- Visual documentation of the problem
- Historical data showing when similar issues occurred
- Previous fixes and their outcomes
- Input from across operational functions
A centralized approach creates a single source of truth. The key is ensuring everyone sees the complete picture before proposing solutions.
2. Make It Stick Through On-the-job Training
A corrective action plan won't work if operators and frontline workers — you know, the people actually executing the plan, day in and day out — are just told to do it.
When employees understand not just what to do but why they're doing it, they become active participants in maintaining improvements rather than passive followers of procedures (or worse: expert pencil-whippers).
A more effective approach focuses on training at the point of use. On-the-job training can prevent recurrence by:
- Building confidence and compliance by combining hands-on practice with real-world settings, not hypothetical what-ifs in a classroom
- Reducing errors through contextualized training at the moment a potential problem or issue comes up — not weeks or months later
- Ensuring process adherence whether you’re executing a task for the first time or the thousandth time
- Decreasing rework by verifying competency before new or updated processes go live
- Providing records that show due diligence when you’ve got external or third-party auditors in the mix
- Turning mistakes into learning opportunities and motivate employees to continuously improve
3. Validate Effectiveness Through Systematic Feedback
Validation isn't a one-time event. It’s an ongoing process that requires systematic attention and crystal-clear metrics. Organizations often fall short by treating validation as an afterthought rather than an integral part of the corrective action process.
A structured validation approach will have:
- Both quantitative and qualitative KPIs to measure success
- Scheduled effectiveness checks at 30, 60, and 90 days (at least)
- Automated data collection to monitor key parameters
- Cross-functional review of outcomes and adjustments as needed
Putting It All Together, Digitally
The most effective solutions integrate the above three elements into a digital system with connected workflows, instead of having siloed — or even worse, paper- or Excel-based — processes. (See “why most corrective actions fail” above.) Digital platforms can streamline this by:
- Connecting quality data to production systems
- Making information accessible where work happens
- Automating follow-up and verification tasks
- Providing visibility into action status
Digital layered process audits (LPAs) can help by providing multiple levels of verification from operators to management that corrective actions remain effective over time. LPAs also truly close the loop on non-conformances by connecting the dots from the initial finding of an issue to ongoing validation that the fix is both sustained and sustainable.
Put the pieces together, and manufacturers will be able to break the cycle of recurring problems, decrease risk, and watch their productivity soar.
Josh Santo is the Director of Industry Strategy & Solutions at Ease.io. He has spent over a decade helping manufacturers deploy digital technologies across the frontlines of their operations. He partners with manufacturing leaders to leverage software and technology that help them optimize safety, quality, and production processes.
The content & opinions in this article are the author’s and do not necessarily represent the views of ManufacturingTomorrow
Comments (0)
This post does not have any comments. Be the first to leave a comment below.
Featured Product
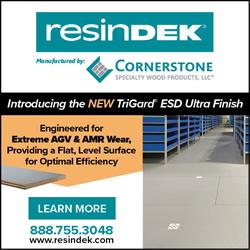