In the wake of the global COVID-19 supply chain nightmares, additive manufacturing has significant implications for improving supply chain resiliency for many manufacturing companies. This is especially the case for companies using a just-in-time methodology.
Goodbye Globalization: Why the Post-Pandemic Supply Chain Needs Additive Manufacturing
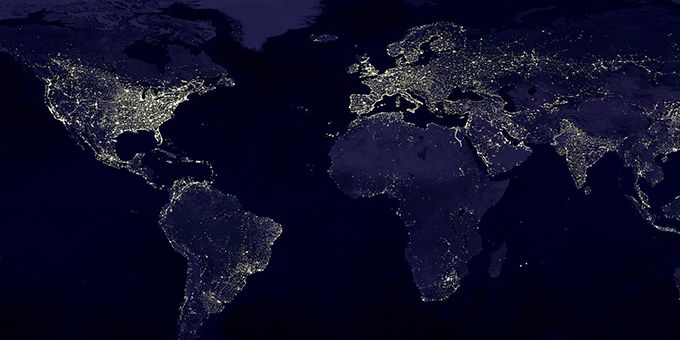
Article from | Marla Keene, Tech writer for Turbine Industrial
In 2011, the New York Times ran an article entitled “The Wow Factor of 3-D Printing.” Although the story had some warnings about the limitations of consumer printing, it rushed on to say “a true 3-D printer craze has started to take hold of the techno-hobbyist clan.” The following paragraphs enthused over the variety of interesting little knick-knacks one could make, from napkin rings to embossed images of beloved children.
A few years later Stratasys’ MakerBot stock tumbled dramatically, the product imploded, and for many consumers the 3-D printing revolution was over.
Meanwhile, additive manufacturing went quietly along, building its customer base and expanding its capabilities. The last years have seen new additive technologies developed, more materials added to the 3D-creation palette, and more industries exploring how additive manufacturing can improve their processes. In fact, growth in the market is strong, with forecasts of 30% growth by 2025.
In the wake of the global COVID-19 supply chain nightmares, additive manufacturing has significant implications for improving supply chain resiliency for many manufacturing companies. This is especially the case for companies using a just-in-time methodology. As companies consider post-COVID adjustments to their sourcing, they must decide how to balance traditional pull-based management strategies against such resiliency opportunities.
The Impact of COVID-19 to Pull-based Production Systems
Pull-based production systems and processes like 5S, Six Sigma and Kanban have been recommended and widely used manufacturing methodologies for decades. These just-in-time pull-based production systems reduced inefficiencies and limited inventory to demand-determined levels.
But such systems have long relied on secure supply chain management. Without agility and diversity, a hiccup caused by international logistics problems, labor problems at a downstream supplier, or transportation issues anywhere along the way have had a disastrous effect on the on-time delivery of goods.
In the wake of the COVID-19 pandemic, some manufacturers saw all these calamities occur one on top of each other in a matter of weeks. Others found themselves competing with labs and hospitals across the globe as the medical community ramped up their fight against the virus for basic but necessary raw materials needed for the manufacture of goods. Without flexible options and relying on a single geographic source for key products, many companies are still working to resolve issues caused by these disruptions.
This is not to imply that just-in-time manufacturing is itself flawed. But the highly sophisticated and vulnerable nature of interlinked, global supply chains has vastly increased the risk for disruption to manufacturers who employ such pull-type management systems. These risks were unmasked by the pandemic. Such problems could arise again from lesser issues like labor disputes, regulatory changes, war, or even supplier bankruptcy.
But a repeat of 2020 problems can be averted now through proper planning. Risk can be limited by the application of resiliency-boosting technologies to the supply chain, including additive manufacturing. This offers a number of benefits.
What is Additive Manufacturing
Unlike traditional manufacturing that typically subtracts from raw materials (a wood block, a steel sheet, etc) to reveal the desired form, additive manufacturing creates an object layer by layer. However, this is a simple explanation of AM that doesn’t begin to encompass the variety of processes that actually ‘live’ under that heading. These include
-
3DP Binder Jetting. 3DP selectively deposits and joins a liquid binding agent with powder particles.
-
Digital Light Processing, or DLP. DLP is similar to SLA, but instead of using a laser to cure resin point by point, DLP uses an LED digital micromirror to flash cure an entire layer all at once.
-
Fused Deposition Modeling, or FDM. FDM builds models using thermoplastic materials injected onto a platform via indexing nozzles. The polymer material laid down hardens before the application of the next layer.
-
Multi-Jet Modeling, or MJM. MJM uses 3-D CAD data to create a plastic model using a printhead on an X/Y/Z axis that is then cured with a UV lamp. This rapid prototyping method is successfully used with a number of composite materials.
-
Stereolithography, or SLA. SLA has been around since the 1980s. It offers intricate details and high dimensional accuracy. However, SLA parts may be brittle.
-
Selective Laser Sintering, or SLS. SLS was one of the first AM techniques, using a high-powered laser to fuse together small particles of a powdered polymer. This has now splintered into selective laser melting (SLM), direct metal laser sintering (DMLS), and other powder bed fusion technologies.
How 3D Printing is Changing JIT Supply Chains
We may look back on 2020 and see it as marking the end of the global supply chain. While previous trends like 2018 trade wars between China and America and earlier slowdowns in foreign investment may have marked coming limitations, the COVID-19 pandemic has been the primary disruptor. Months into the pandemic we are still seeing disruptions and fracturing to long-established supply chains.
This fracturing may become the norm. Certainly, many are reconsidering any sourcing from China. This global uncertainty begs the question: how do manufacturers best respond to logistical challenges brought about by unexpected disruptions?
Additive manufacturing may be key to meeting those challenges. The quick prototyping ability of AM allows for a rapid response to any sort of demand, including emergency changes to the supply chain. Additionally, the flexibility and customization aspects of 3D printing allows for changes as needed to products produced. The decentralized nature of this type of manufacturing will also allow for less dependence on faraway sources for upstream goods and instead put the source at or nearby the point of delivery.
Manufacturers who run with just-in-time standards in place maintain an emphasis on eliminating waste, reducing costs, and improving quality. These objectives line up well with 3D printing capabilities. This technology will allow manufacturers to remove variables like time and transportation. It will allow for increased flexibility on the timing of parts creation, meaning storage costs can drop to near zero. And it allows for a continual feedback loop where corrections can be made in near real time, improving products almost as soon as the need arises.
About Marla Keene
Marla Keene is a tech writer for Turbine Industrial. She writes about AI, drones, AR/VR, and how technology is changing today’s manufacturing floor. Her articles have been featured in Servo Magazine, Medium, and many industry publications.
The content & opinions in this article are the author’s and do not necessarily represent the views of ManufacturingTomorrow
Comments (0)
This post does not have any comments. Be the first to leave a comment below.
Featured Product
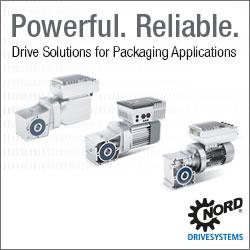