Satair, an Airbus services company, wanted to expedite aircraft maintenance through on-demand tools manufacturing. Fast Radius worked with Satair to deliver an innovative multi-process manufacturing solution that has the potential to transform the aerospace market.
MAKING FASTER FLIGHT MAINTENANCE POSSIBLE
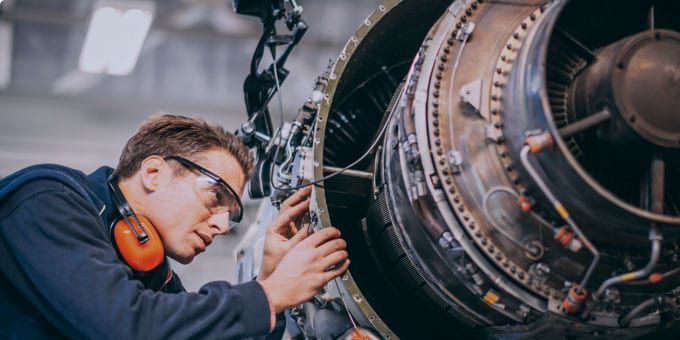
Case Study from | Fast Radius
THE CHALLENGE: GETTING GROUNDED AIRCRAFT BACK IN FLIGHT FASTER
Satair serves customers in the global aerospace value chain by delivering parts management, distribution, and support solutions.
The company prides itself on anticipating individual customer needs. In aircraft maintenance, that means delivering the parts and tools customers need to get aircraft back in the air quickly. Satair envisions a world with fewer flight delays, faster travel, and the highest standards of safety.
THE PLAN: Exploring Advancements In The Manufacturing Supply Chain With The Virtual WAREHOUSE
To meet Satair’s goals, Fast Radius tested and implemented several digital solutions during this innovation project. The teams used digital manufacturing to:
- Reduce the lead time for tool orders
- Meet the previous high standards of quality and safety
- Improve sustainability
The solution started with modern additive manufacturing techniques that could yield tools that met the rigorous functional requirements in record time. Tools redesigned for additive also have lower overall mass, which improves handling and transport costs and can have a positive impact on reducing carbon dioxide emissions.
Making manufacturing faster was one part of the solution. Speeding up logistics was the other. New tools in digital manufacturing and additive technology are blurring the lines between manufacturing and logistics, making faster, more sustainable turnaround times possible. One of the possible tools some companies use to speed up logistics is the Fast Radius Virtual Warehouse™.
QUICK LOOK: WHAT IS THE FAST RADIUS VIRTUAL WAREHOUSE?
Unique to additive manufacturing, the Fast Radius Virtual Warehouse stores digital part files in the cloud, potentially allowing for the production of products on-demand, whenever and wherever they are needed. By perfectly matching need with supply, the Virtual Warehouse prevents waste and reduces materials usage.
THE SPEED TO PRODUCTION PILOT: FROM WEEKS TO DAYS
Over the course of this project, Fast Radius manufactured, inspected, packaged, shipped, and fulfilled two complete tools in under 48 hours. The pilot hinged on Fast Radius’s logistics partnership with UPS, which allowed Fast Radius to ship parts from its factory in Chicago to Satair’s distribution facilities in Hamburg, Germany in less than 48 hours from receipt of order to delivery.
MAKING IT POSSIBLE: TOOL REDESIGN AND RAPID ITERATION
01. A MULTI-PROCESS SOLUTION
The Fast Radius team recommended a multi-process approach that included both additive manufacturing processes (HP Multi Jet Fusion) and traditional ones (CNC) to give Satair the best price, reduce the total part numbers in the bill of materials (BOM), improve design robustness, and enable the integration of new functionalities.
02. RAPID DESIGN ITERATION
During the project, Satair and Fast Radius collaborated to investigate ways to redesign and improve selected aircraft maintenance tools to ensure manufacturability with additive technology. The teams worked closely to create new geometries for the tools that reduced material usage and improved functionality. They achieved new efficiencies through assembly consolidation, lightweighting, and unique design architectures only possible with additive manufacturing. During this process, Fast Radius teamed up with Satair engineers through intensive working sessions that employed rapid prototyping with production-grade technologies and used a combination of digital simulation and physical testing to quickly iterate and refine the designs.
03. HP MULTI JET FUSION TECHNOLOGY
The HP Jet Fusion 580 Color 3D Printer was selected for this application due to the machine’s ability to produce full-color parts with optimal mechanical properties. The machine was able to produce multiple design iterations in the same time it would normally take to print a single part, which significantly cut down on the development time. Because of the harsh environments these tools would need to endure, the material selected was HP 3D High Reusability PA 12 — an engineering-grade thermoplastic with excellent chemical resistance to oils, greases, aliphatic hydrocarbons, and alkalies.
04. ACHIEVING HIGH AEROSPACE STANDARDS
Satair operates at the highest level of safety and security, so any product or supply chain changes need to maintain that standard. For example, in addition to its existing AS9100 certification for aerospace quality, Fast Radius implemented a rigorous production part approval process to ensure the company sent consistent, quality parts to Satair. Fast Radius developed ongoing control plans for each tool and implemented a continuous improvement plan to ensure that the parts continue to meet rigid aviation standards.
DISCOVERING THE VALUE OF COLOR 3D PRINTING
Through its partnership with HP, Fast Radius gave Satair access to technology that could enhance their production process. For example, Fast Radius used the HP Jet Fusion 580 Color 3D Printer to print Satair tools in full color, which improves safety by ensuring that tools are not left behind after use. Color also introduces new ways to convey information, such as company logos, part numbers, serial numbers, or even scannable QR codes printed directly on to the tool.
THE TOOLS: Redesigned For Faster Flight Maintenance
FLAP ZERO LOCKING TOOL
Used for flap maintenance in the A320 cockpit, locking the Flaps control lever in Zero position.
- Assembly reduced from six components to two
- 50% lead time reduction
GAGS TOOL PADS
Used for main landing gear maintenance on the A380, gagging the main landing gears.
- Improved strength-to-weight ratio
- 60% mass reduction
PINTLE BEARING ALIGNMENT TOOL
Used for bearing in the rear spar prior to installing it during Main Landing gear installation.
- Assembly reduced from four parts to two
THE RESULTS: A FASTER, MORE SUSTAINABLE FUTURE FOR AIRCRAFT MAINTENANCE
Satair and Fast Radius are in the early days of exploring what’s possible with the Virtual Warehouse, enabled by HP’s Multi Jet Fusion 3D printing technology and a logistics partnership with UPS for the delivery of parts produced during this pilot. So far, outcomes from this program point towards a bright future where Satair will deliver world-class innovative solutions to its aircraft maintenance customers. Satair and Fast Radius are investigating further ways of working together to redesign more tools with additive manufacturing.
As awareness increases with other aerospace manufacturers, airlines, and MROs, the benefits of faster, more sustainable aircraft maintenance will begin to transform the entire industry.
The content & opinions in this article are the author’s and do not necessarily represent the views of ManufacturingTomorrow
Comments (0)
This post does not have any comments. Be the first to leave a comment below.
Featured Product
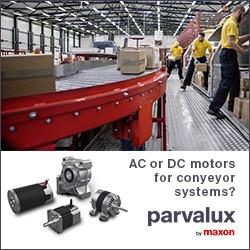