Manufacturers may need to go through calibration processes to ensure consistent results with every use of a tool or piece of equipment that can or should be calibrated.
What You Need to Know About Calibration
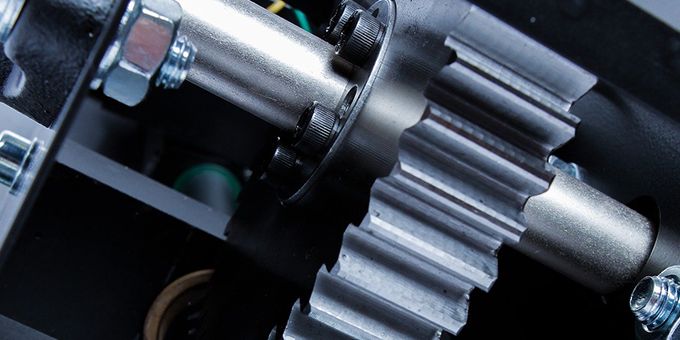
Scott Huntington | Off The Throttle
In the manufacturing sector, quality control is essential for a company's success. Businesses often use numerous pieces of equipment and tools to keep their performance and output at high levels. However, manufacturers may need to go through calibration processes to ensure consistent results with every use of a tool or piece of equipment that can or should be calibrated.
What Is Calibration?
Calibration simply means comparing the performance of a tool against a reference standard or an item that has a higher level of verified accuracy. Then, the goal is to measure the difference between the two. If there is a significant difference between what's shown from the tested tool and the one with known accuracy, calibration is likely needed. It involves adjusting the assessed tool to increase accuracy and thereby make it more reliable.
What Kinds of Things Do Manufacturers Calibrate?
If a manufacturing plant uses a tool for measurement, there's a good chance it requires periodic calibration. For example, it's necessary to calibrate scales, humidity sensors, thermometers and pH meters. Also, if a company is embracing the Industrial Internet of Things (IIoT) by using sensors, those need calibration to perform accurately too.
In short, if a company uses an instrument to verify product quality or inspect components, it needs calibration. A lack of calibration could produce unsafe results, eroding public trust in a company and damaging the brand's reputation.
What Are the Main Types of Calibration?
The types of calibrations a manufacturer performs depend on the kind of equipment the company uses in its operations. However, here are some of the most widely used kinds of calibrations:
Pressure Calibrations
A pressure gauge measures the intensity of a fluid. Thus, tools associated with gas and hydraulic pressure often require pressure calibration. Both analog and digital pressure gauges require calibration, as well as barometers and transmitters. Hydraulic systems are also designed to work within a specific pressure range, so any indicator used must be rated to perform within those parameters.
A pressure gauge can alert operators to leaks or abnormal changes in pressure that require prompt troubleshooting. In essence, the pressure gauge gives a glimpse into the operations of a hydraulic system, meaning a lack of calibration for that measurement device could cause costly and disruptive complications. Users often depend on pressure calibrators to check the performance of an uncalibrated system and see how it compares to the accurate one.
Pressure calibrators typically show their accuracy as a ratio. For example, a pressure calibrator with a 4:1 ratio is four times as accurate as the device it is calibrating.
Electronic Calibrations
This is a type of calibration necessary for electronic tools, such as those used in the aerospace, pharmaceutical and defense industries. Electronic calibrations are also called electrical calibrations because they measure devices that control the flow of electrical currents.
Calibration technicians adjust electronic equipment so that its output meets national or international standards. Plus, calibration requires examining and adjusting each electronic component separate from the overall system that contains it.
Additionally, electronic calibrations may be the bench or field variety. Choosing the most appropriate option in that regard typically depends on whether the device with the electronics to calibrate is already in use.
If so, movement and transport, such as while sending the device to an off-site calibration company, could affect the instrument. Then, bench testing is likely the smartest choice. However, if a measurement device is getting factory shipped from a laboratory, bench testing is the process through which calibration occurs.
Mechanical Calibration
Facilities that perform mechanical calibration are usually temperature-controlled, and they allow testing aspects including torque, mass and vibration. Scales and accelerometers are two tools that require mechanical calibration.
Also, many companies hire mechanical calibration technicians to assist with the task during product development and testing. These professionals use a variety of tools, from oscilloscopes to calipers, while performing calibration. They must also travel frequently, particularly if a manufacturer has on-site controlled buildings used for mechanical calibration.
Temperature and Humidity Calibrations
Temperature and humidity calibrations are like the mechanical variety in that they also occur in tightly controlled environments. Thermal cameras, weather stations and digital temperature probes are a few examples of items that need these kinds of calibrations.
It’s especially important to carry out the calibrations on a recommended schedule if temperature and humidity inaccuracies could cause catastrophes such as spoiled food, ruined medications or warped material.
What to Know About Instrument Calibration and Traceability
A concept called metrological traceability relates to a calibration hierarchy whereby a so-called traceability pyramid has the reference standards with the highest accuracy at the top. However, the accuracy decreases as the uncertainty of measurement — the margin of error associated with each reference standard — goes up. The goal is for the measurement or value of a reference standard to link back to a national or international standard.
The International System of Units (SI) is at the top of what people sometimes refer to as a traceability pyramid. There are also primary calibration laboratories called National Metrology Institutes (NMIs) that carry out the most accurate calibrations. They're situated at the part of the pyramid below SI.
The pyramid continues downward to indicate several more levels. The main thing to remember is that any measurement should always be traceable back to a national or international standard. Some manufacturers may even need to guarantee the traceability of their calibration before entering into a new contract with a customer. The client may insist that the manufacturer uses adequately and regularly calibrated instruments before agreeing to create a partnership.
If a manufacturer receives a calibration certificate for its instruments, that document should indicate the traceability specifics. For example, it might say that the standards are traceable to the National Institute of Standards and Technology (NIST).
How Does Proper Instrument Calibration Help Manufacturers?
After learning about the broad types of instrument calibrations, manufacturers might wonder about the specific ways that calibration could benefit them.
First, it can enable manufacturers to feel confident that their tools are working as advertised. The owner's manual for a manufacturing tool that requires calibration should provide details about tolerances. It is an expression of the permissible amount of deviation between the known standard and the output of the tested device.
Companies that provide calibration services generally guarantee that a device will remain calibrated correctly in the operating conditions specified in the owner's manual for a particular period — such as six months. However, the documentation that comes with a device should also clarify how often calibration should happen. If a user notices that calibration is necessary more frequently than stated, that outcome may indicate a flaw with the measurement device.
Calibration can also boost a manufacturer's efficiency, particularly if a company takes care to apply the same calibration techniques to a particular instrument each time. The quality of measurement decreases over time with normal use. If not corrected through calibration, the problem could cause subpar products to reach the marketplace and eventually tarnish customers' perceptions.
Properly calibrated instruments can also reduce downtime for a manufacturer. If a tool shows the correct readout, company representatives can quickly assess whether everything is as it should be or if it's necessary to take a machine out of service for repairs. But if an instrument is not calibrated, it could provide inaccurate statistics associated with a machine and potentially cause disruptions in production.
Calibration: A Must for Modern Manufacturers
This overview explains the broad types of calibrations and why they apply to the manufacturing sector. Instruments that get calibrated on the right schedule and by a competent professional could help a company prosper. Conversely, instruments that are calibrated incorrectly or infrequently could cause confusion, offer misleading results and even compromise customer safety.
The content & opinions in this article are the author’s and do not necessarily represent the views of ManufacturingTomorrow
Comments (0)
This post does not have any comments. Be the first to leave a comment below.
Featured Product
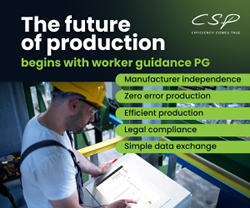