2016: Why Manufacturers Should Embrace Real-Time Data
New technologies such as IoT attract the best minds in business, but also a lot of unproven and even untested ideas. Proceed with care.
The Jubilant Team of Winjit wins appreciation for their Innovative IOT Gateway at the Illustrious Mobile World Congress, Barcelona
The gateway enables built-in Analytics Services, to Develop solutions and Industry prototypes hence channelizing the best of IoT ecosystem
Becoming the Factory of the Future: How to Prepare Now for the Industrial Internet of Things
The Internet is not going to hit the factory all at once; the transition to global connectivity will be gradual. In the meantime, businesses have a chance to prepare their operations to integrate seamlessly with this new era of industry by taking steps now to implement digital, automated, connected devices and services.
Nobilia uses IoT to create smart factory
Kitchen maker Nobilia has rolled out IoT and automation systems in its German factories to enable real-time tracking of furniture as it progresses through the manufacturing process.
The company, which has distribution in Australia, is using Beckhoff automation technology that is powered by Intel processors.
A barcode that is attached to furniture is encoded with details including processing steps, components required to be added to complete it, and logistics information such as where the finished product is to be delivered.
“Each processing machine scans the barcode and retrieves the associated machining data from a central database. Data connecting the whole factory together makes it possible to produce 2700 kitchens daily,” Intel said in a blog post.
“Through real-time tracking enabled by Intel IoT technologies, Nobilia knows exactly where each part is in the production process at any time.
“If one of the manufacturing lines shuts down, parts are automatically rerouted to another line.”
Who Is Adopting IoT and Why?
We all know the Internet of Things is set to revolutionize the manufacturing industry but how will this happen? A new study of manufacturers across 12 different countries has provided quantified answers to the questions the industry is asking.
Five Reasons Why Manufacturers Are Embracing IoT
The Internet of Things (IoT) is enabling manufacturers to be more efficient, productive and profitable in the face of increased competition worldwide. We look at five reasons why manufacturers are betting big on these new technologies.
Records 46 to 51 of 51
Featured Product
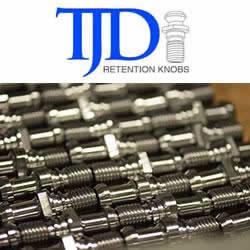
T.J. Davies' Retention Knobs
Our retention knobs are manufactured above international standards or to machine builder specifications. Retention knobs are manufactured utilizing AMS-6274/AISI-8620 alloy steel drawn in the United States. Threads are single-pointed on our lathes while manufacturing all other retention knob features to ensure high concentricity. Our process ensures that our threads are balanced (lead in/lead out at 180 degrees.) Each retention knob is carburized (hardened) to 58-62HRC, and case depth is .020-.030. Core hardness 40HRC. Each retention knob is coated utilizing a hot black oxide coating to military specifications. Our retention knobs are 100% covered in black oxide to prevent rust. All retention knob surfaces (not just mating surfaces) have a precision finish of 32 RMA micro or better: ISO grade 6N. Each retention knob is magnetic particle tested and tested at 2.5 times the pulling force of the drawbar. Certifications are maintained for each step in the manufacturing process for traceability.