In the industrial maintenance space, knowledge is key for employee retention
Imagine tasking a member of your industrial maintenance team with a series of repairs or preventative maintenance tasks. At first glance, this might seem like an appropriate request. After all, industrial maintenance professionals are entrusted first and foremost with keeping equipment and facilities in proper condition. It’s the core of what they do.
But imagine issuing these tasks, then refusing to provide employees with the tools they need to do the job well—no hand tools, no diagnostic instruments, not even any blueprints to better understand how complex equipment functions. Absent the right tools in their toolbox, even the best industrial maintenance professionals may feel like they are being set up for failure. In this scenario, it would be little wonder if these professionals experienced a precipitous drop-off in engagement and morale.
If this principle holds true for physical tools, it’s equally important for knowledge, skill formation, and professional development—all of which are essential for industrial maintenance employees to feel supported in their work and equipped to do the best job they can.
An investment in ongoing education is really an investment in your employees, and it can significantly boost engagement, morale, and retention. By contrast, employees who are not given space to learn new things or to broaden their skill sets may end up leaving the organization altogether.
How training addresses turnover
Investing in training is essential for organizations that want to retain both new and tenured workers. Ongoing development keeps industrial maintenance teams engaged, builds loyalty, and shows employees their growth matters, making them far more likely to stay.
There are a number of ways in which training helps team members feel better supported:
- Well-trained employees can show up to new projects feeling confident in their ability to get the job done and fix problems the first time. This prevents feelings of frustration or inefficiency, which no employee wants to experience.
- Proper training also helps employees work in a way that’s safe and fully compliant with relevant regulations. In other words, making an investment in training shows employees that you care about their well-being.
- By equipping employees to complete projects efficiently, you position them to cross more items off their to-do list and chalk up more “big wins” each day, which can significantly boost their confidence and help them feel like rock stars within the workplace.
Building a culture of continuous training
Recognizing the value of continuous training and skills development is an important first step. From there, a strategic and structured approach is required to ensure that training is a real part of company culture—not just a one-time occurrence.
To make learning a never-ending process for your industrial maintenance team, consider a few guidelines and best practices:
- Prioritize accessibility. Busy industrial maintenance professionals don’t have hours to spend in the classroom each day. Thankfully, today’s advanced training technology provides plenty of flexible ways to incorporate micro-learning throughout the workday.
- Provide practical application. Industrial maintenance is an inherently hands-on profession, so connecting training to real-world application is a must. Simulations and on-the-job mentorship can be essential.
- Recognize progress. To keep employees motivated, celebrate achievements, certifications, and skill advancements. This might mean recognition on a companywide goal board, deposits into a tool account, or other incentives.
Considering the core elements of a structured training program
Beyond these steps, it’s important to bear in mind the elements most essential for creating an impactful learning environment. Three areas warrant particular focus:
- A well-designed onboarding process. Training begins even before employees get into the nitty-gritty of their work. Structured onboarding ensures that employees feel ready to begin their work with confidence and start contributing to the team almost immediately.
- Ongoing opportunities for skill formation. Onboarding should be considered the start, not the culmination of employee training. Schedule simulations, training sessions, and assessments at regular intervals, keeping employees sharp and engaged.
- A clear sense of progression. Finally, be certain that employees see a connection between training and career growth—and that they understand how mastering new skills can help them achieve professional milestones.
The bottom line: Industrial maintenance can be challenging. Team members need to feel like they have every necessary tool to succeed, and that includes knowledge. A robust investment in training can provide the tools they need and let employees know that you’re betting on their ongoing success. That’s the key to having an efficient team, and it’s a must for keeping early turnover rates under control.
Tim McDaniel is a Solutions Consultant at Interplay Learning, the leader in immersive training for the skilled trades.
Comments (0)
This post does not have any comments. Be the first to leave a comment below.
Featured Product
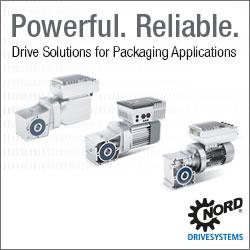