What Does Digital Manufacturing Mean and How Can We Move Toward It?
Manufacturing is a fast-moving industry, and as such, it’s prone to buzzwords. Phrases like “Industry 4.0” and “digital manufacturing” populate discussions about the sector, but their use can easily outgrow understanding of what they mean.
Digital manufacturing is more than a buzzword. It’s a movement that could redefine the industry, pushing it toward new levels of productivity, efficiency and accuracy. To achieve these benefits, though, manufacturers need to take the time to understand what it actually means. Here’s a closer look.
What Is Digital Manufacturing?
Put simply, digital manufacturing is the application of automated technologies to the entire process. It uses tools like the Internet of Things (IoT), digital twins and data analytics to create interconnected, cohesive and optimized production from start to finish.
An excellent real-world example of digital manufacturing and its benefits is the Siemens plant in Amberg, Germany. The facility began digitizing in 2010, and over the next decade, 75% of its processes became digital or automated, compared to just 25% before. This mass digitization resulted in a remarkable 1,400% increase in productivity.
Siemens used IoT sensors and data analytics to create a digital twin of the factory. By analyzing and adjusting various parts of this model, the facility could see where inefficiencies were and which changes would have the greatest impact. As the factory implemented more digital technologies, its data grew, providing more insight and further improvements.
Steps Toward Expanding Digital Manufacturing
Many factories use technologies like the IoT, but true digital manufacturing applies them to virtually every operation. Each process is interconnected in the digital factory. Reaching this level of technological implementation is no small feat, so here’s how the industry can move in that direction.
Determine Highest-Value Use Cases
Digital manufacturing technologies can carry high upfront costs, and this transition is often disruptive. Manufacturers should slowly and gradually implement these technologies to minimize disruption, starting with the highest-value use cases. Up to 60% of typical production processes don’t add value, but some have more potential for improvement.
Facilities should analyze their operations and successful digitization efforts in other factories to determine the highest-value changes. After fixing their most glaring issues with new technologies, they can move on to different use cases. This gradual, analytics approach to transformation will ensure more long-term success.
Invest in Upskilling and Reskilling
As the industry becomes increasingly digitized, the role of human workers in the sector will change. Many current jobs will become automated, and new positions requiring different skills will open. This could result in simultaneous job displacement and labor shortages unless the sector invests in reskilling.
Digital manufacturers will need fewer physical laborers and more IT personnel. They can train their workforce for this change by establishing programs to help current workers learn IT skills. If manufacturers can successfully reskill their workforce, they can avoid labor shortages and retain dedicated staff.
Improve Cybersecurity
Another significant challenge with digital manufacturing is the cybersecurity vulnerabilities it creates. Manufacturing has already become one of the most targeted industries for ransomware, with cyberattacks targeting one in five manufacturers. Given these threats, cybersecurity in the sector must improve for digital manufacturing to grow.
As manufacturers implement more digital technologies, they should ensure they also expand their security. IoT safety and employee training are two of the most crucial areas for consideration here. As industry standards for cybersecurity improve and grow, facilities can move into digital manufacturing with confidence.
The Future of Manufacturing Is Digital
Digital manufacturing has too much potential for the industry to ignore. These technologies and processes will eventually define the sector, but how fast that transition happens is up to manufacturers.
The industry must start preparing now for these future shifts. Careful, more thought-out transitions will minimize risks and maximize returns. Digital manufacturing will then live up to its full potential.
Comments (0)
This post does not have any comments. Be the first to leave a comment below.
Featured Product
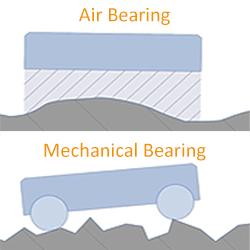